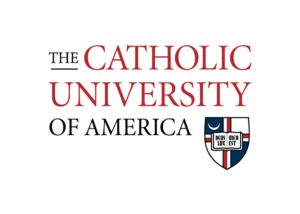
Arapahoe Community College is a public institution located in Littleton, Colorado. It was established in 1965 and is one of the oldest community colleges in Denver. It offers several undergraduate programs. If you are considering pursuing an ACC diploma, you can read on to learn about the courses you will need.
Obtaining an ACC Degree
An ACC Degree is a great way for you to jumpstart your career and gain a competitive edge in the job marketplace. There are many academic programs offered by the college that can prepare students for employment immediately or transfer to a four year university. There may be prerequisite courses that you need before you are allowed to enroll in a program. Admission requirements will vary depending on the program. Both returning students and newcomers are welcome at the college. They offer Associate in Arts (AA), Bachelor of Science (BS), degrees.
The college offers over 100 programs in 10 subjects. Associate of Arts degrees, university transfer credits and career-technical certificates can be earned. Austin Community College has several options for highschool students. Coursework can be offered in a variety different settings, such as hands-on labs or classrooms. In addition, you can take advantage of the college's career services and attend cultural events and field trips while earning your degree.
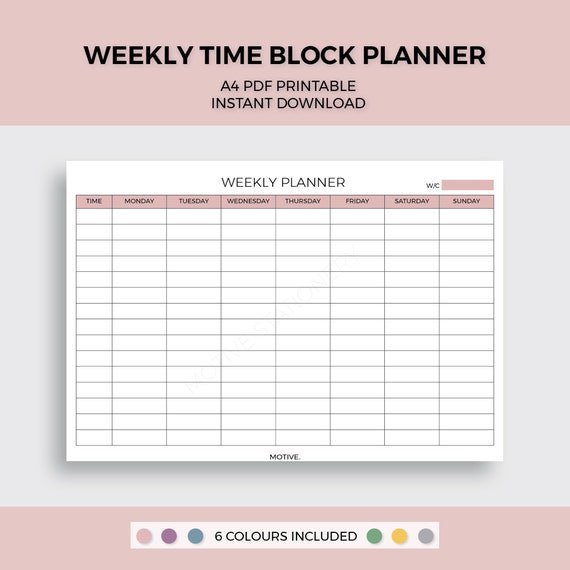
No courses required
To earn a degree at Arapahoe Community College, students must take certain courses. These courses are outlined in the college's Catalog. Arapahoe also reserves the right to change these policies at any time. For the most recent information, students are advised to visit the college's web site.
The college offers many programs. There are many programs available for Associate of Science degrees. It is possible to also obtain a degree either in Spanish or in a foreign language.
Acceptance into a 4-year university
Arapahoe Community College in Littleton is a Colorado public institution. It has an enrollment of 11,544 students and uses a semester-based academic calendar. It offers many degree programs in 16 different areas. Many of these programs can be transferred to 4-year colleges.
ACC is a wonderful place to begin your career or continue your education. You can take courses online or at your high school campus. You can even earn your workplace credential while you study for your degree.
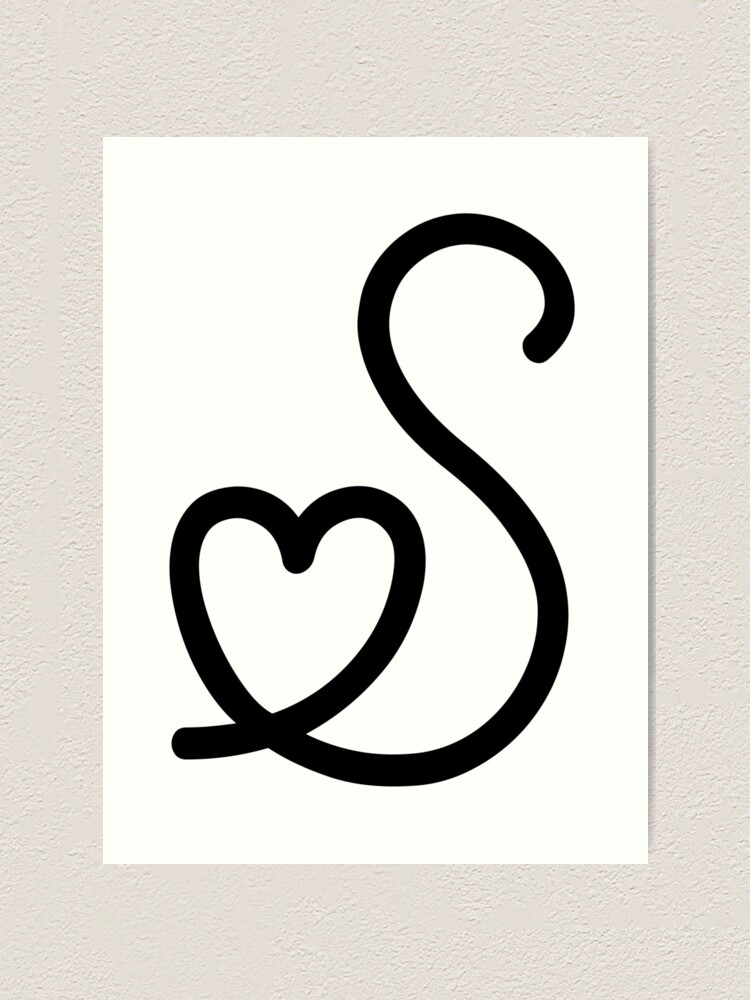
Study abroad options with ACC
Arapahoe Community College has many options for students who wish to study abroad. These programs feature guided learning, cultural engagement, and program immersion. These programs are designed to enhance students' professional and academic skills. A Study Abroad Club can also be found at the college. This club meets regularly to encourage international understanding as well as cultural diversity.
The college offers many study abroad options, ranging from programs in Western Europe to those in the far reaches Asia. It has offered programs in Australia and Costa Rica, as well as Vietnam and Beijing. Many programs are tied to particular courses and can often be completed within one week or one semester.
FAQ
How can a manager improve his/her managerial skills?
It is important to have good management skills.
Managers must constantly monitor the performance of their subordinates.
You must quickly take action if your subordinate fails to perform.
It is important to be able identify areas that need improvement and what can be done to improve them.
Why is Six Sigma so popular?
Six Sigma is easy to implement and can produce significant results. It provides a framework that allows for improvement and helps companies concentrate on what really matters.
What is Six Sigma?
It's an approach to quality improvement that emphasizes customer service and continuous learning. The goal is to eradicate defects through statistical techniques.
Motorola invented Six Sigma in 1986 as part its efforts to improve manufacturing.
The idea spread quickly in the industry. Today many organizations use six-sigma techniques to improve product design.
What role does a manager play in a company?
Each industry has a different role for a manager.
In general, a manager controls the day-to-day operations of a company.
He/she ensures that the company meets its financial obligations and produces goods or services that customers want.
He/she ensures employees adhere to all regulations and quality standards.
He/she plans new products and services and oversees marketing campaigns.
Statistics
- The BLS says that financial services jobs like banking are expected to grow 4% by 2030, about as fast as the national average. (wgu.edu)
- Hire the top business lawyers and save up to 60% on legal fees (upcounsel.com)
- This field is expected to grow about 7% by 2028, a bit faster than the national average for job growth. (wgu.edu)
- Our program is 100% engineered for your success. (online.uc.edu)
- 100% of the courses are offered online, and no campus visits are required — a big time-saver for you. (online.uc.edu)
External Links
How To
How do you do the Kaizen method?
Kaizen means continuous improvement. The term was coined in the 1950s at Toyota Motor Corporation and refers to the Japanese philosophy emphasizing constant improvement through small incremental changes. This is a collaborative process in which people work together to improve their processes continually.
Kaizen, a Lean Manufacturing method, is one of its most powerful. Kaizen is a concept where employees in charge of the production line are required to spot problems during the manufacturing process before they become major issues. This will increase the quality and decrease the cost of the products.
The main idea behind kaizen is to make every worker aware of what happens around him/her. Correct any errors immediately to avoid future problems. So, if someone notices a problem while working, he/she should report it to his/her manager.
Kaizen follows a set of principles. We always start from the end product and move toward the beginning. If we want to improve our factory for example, we start by fixing the machines that make the final product. First, we fix machines that produce components. Next, we fix machines that produce raw material. Then, we fix those who work directly with the machines.
This is known as "kaizen", because it emphasizes improving each step. Once we have finished fixing the factory, we return to the beginning and work until perfection.
To implement kaizen in your business, you need to find out how to measure its effectiveness. There are many ways you can determine if kaizen has been implemented well. One method is to inspect the finished products for defects. Another method is to determine how much productivity has improved since the implementation of kaizen.
A good way to determine whether kaizen has been implemented is to ask why. You were trying to save money or obey the law? Did you really believe it would lead to success?
Congratulations if you answered "yes" to any of the questions. Now you're ready for kaizen.