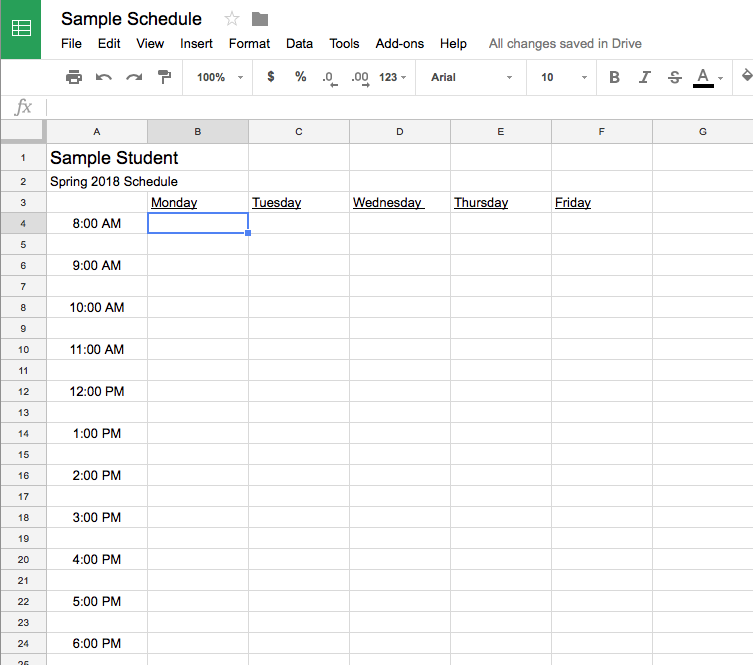
When it comes to transforming old buildings into new ones, you should consider hiring professional turner contractors. However, you should be aware of the cost and benefits of hiring a professional. These are some of the reasons you should hire turner contractors. Keep reading to learn more. Professionals are a great way of ensuring a quality finish on your building. Read on to discover the benefits and costs of hiring a turner contractor.
Turner professionals
A professional contractor is available for any home renovation or major addition. Turner Contracting is known for providing exceptional customer service and quality workmanship. They will create a home that is both functional and beautiful. They can help turn your remodeling dreams into a reality by providing quality home remodeling services across West Central Florida. Learn more about Turner's services.
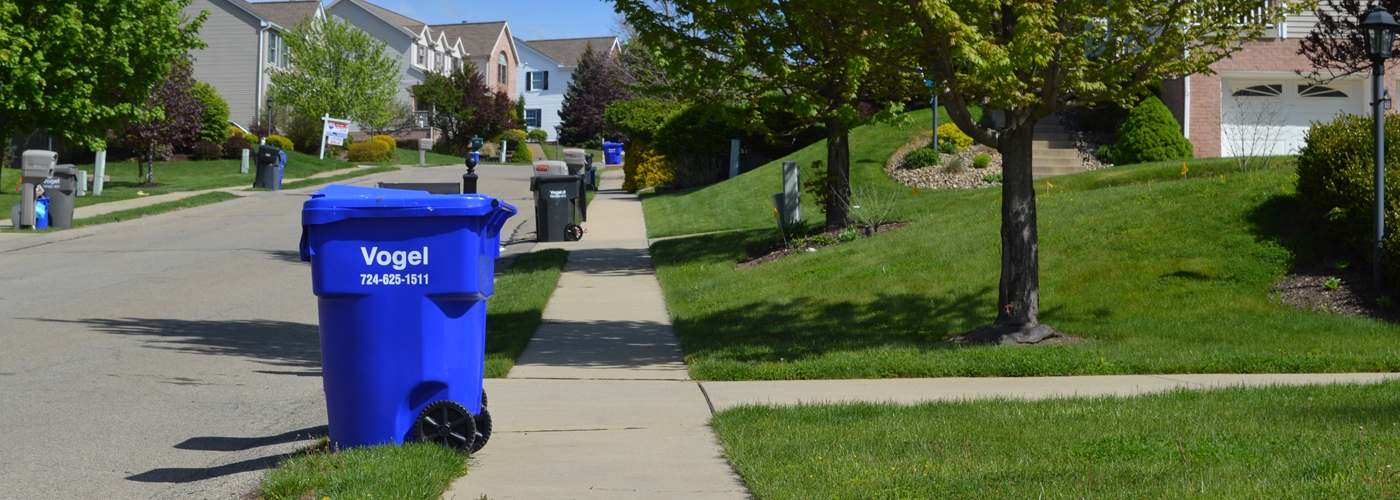
The Turner Construction Company is an American construction company. The company employs more than 5000 people annually and completes over 1,500 construction projects. This company is known as the pioneer in steel-reinforced concreting, which can be used to make safer, stronger and more energy-efficient buildings. The company taps into the creativity and inventiveness of its employees to construct innovative structures. New York City is the headquarters of the company. The company's website offers a range of contact information including a blog in which Sumele discusses architecture. She enjoys reading and cooking.
Hiring professional turner contractors is expensive
It's a smart idea to find a contractor who specializes in turninger construction when you are looking for a general contractor. This type company specializes in large-scale, high-quality projects. This type of company is more likely not to charge hidden fees and offer better rates. There are many choices available, whether you're searching for a general contractor within the Philadelphia region or elsewhere.
There are many benefits to hiring professional turner contractors
Turner contractors are a great choice if your need a contractor for work around the house. Contractors offer a range of benefits to employees. These benefits include 401k Matching, federal Holiday Pay, and 10 sick Days. They also offer vision insurance and health coverage. They also offer generous PTO. They also provide assistance for new employees starting families.
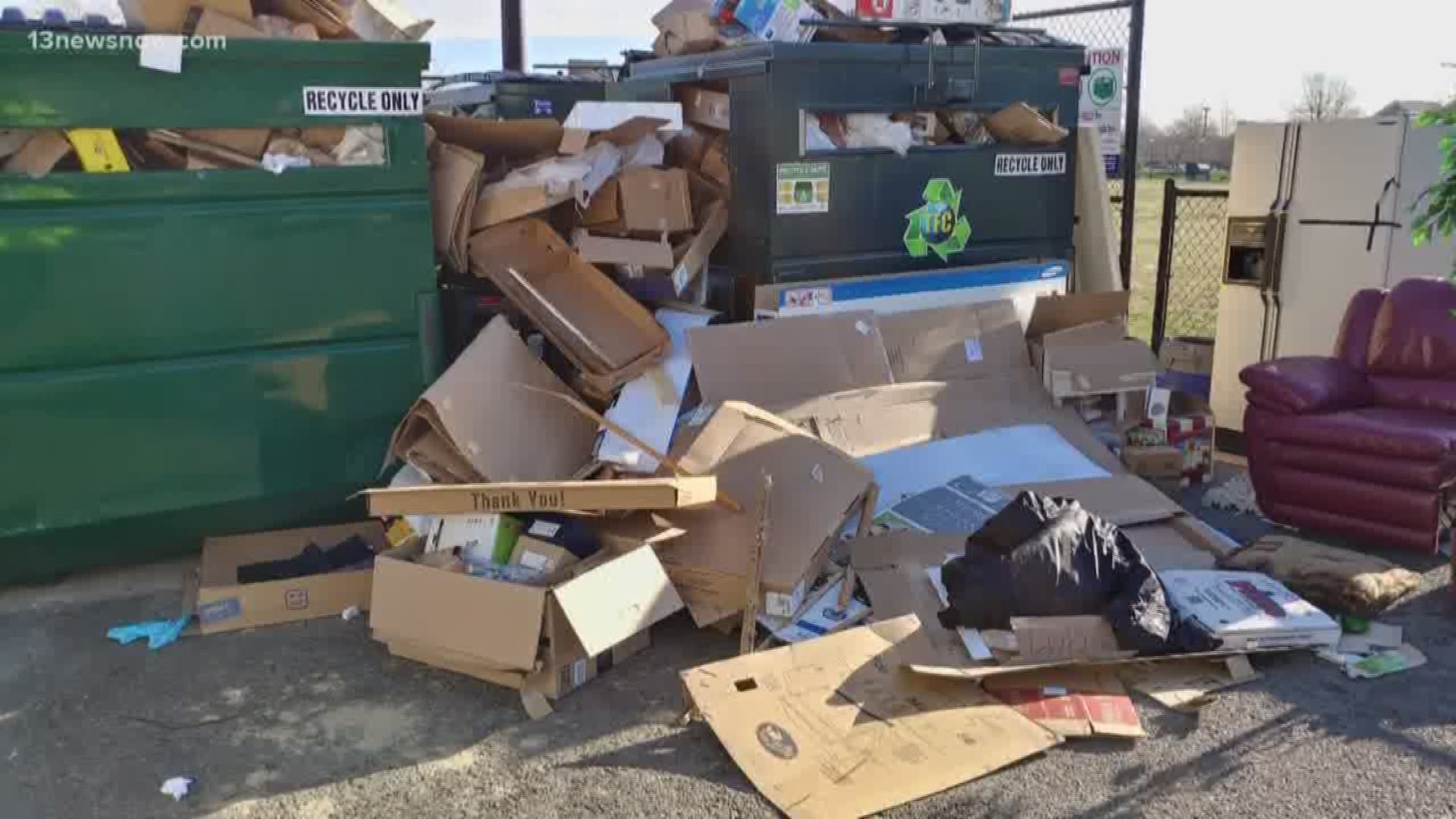
Multiple projects are managed by the C-suite. They ensure that they adhere to ethical and policy guidelines regarding contract negotiations. They also oversee all financial aspects of projects. Turner is a large corporation, so their project managers are often involved in multiple projects at once. These managers have many duties and are responsible in maintaining a positive attitude, and keeping the company's track.
FAQ
What are the steps involved in making a decision in management?
Managers have to make complex decisions. It involves many factors, such as analysis and strategy, planning, execution, measurement, evaluation, feedback etc.
It is important to remember that people are human beings, just like you. They make mistakes. As such, there is always room for improvement, especially if you're willing to put forth the effort to improve yourself first.
In this video, we explain what the decision-making process looks like in Management. We'll discuss the different types and reasons they are important. Managers should also know how to navigate them. The following topics will be covered.
How can we create a successful company culture?
A company culture that values and respects its employees is a successful one.
It's built on three fundamental principles:
-
Everybody has something to offer.
-
People are treated fairly
-
Individuals and groups can have mutual respect
These values are reflected in the way people behave. They will treat others with consideration and courtesy.
They will listen to other people's opinions respectfully.
They will also encourage others to share their ideas and feelings.
A company culture encourages collaboration and communication.
People feel free to express their views openly without fear of reprisal.
They are aware that mistakes can be accepted if they are treated honestly.
Finally, the company culture promotes honesty and integrity.
Everyone knows that they must always tell truth.
Everyone recognizes that rules and regulations are important to follow.
People don't expect special treatment or favors.
What are some common management mistakes?
Sometimes managers make it harder for their employees than is necessary.
They may not assign enough responsibilities to staff members and provide them with inadequate support.
In addition, many managers lack the communication skills required to motivate and lead their teams.
Managers sometimes set unrealistic expectations of their teams.
Managers may prefer to solve every problem for themselves than to delegate responsibility.
How does a manager develop his/her management skills?
By practicing good management skills at all times.
Managers must continuously monitor the performance levels of their subordinates.
You must quickly take action if your subordinate fails to perform.
You should be able pinpoint what needs to improve and how to fix it.
Statistics
- Hire the top business lawyers and save up to 60% on legal fees (upcounsel.com)
- UpCounsel accepts only the top 5 percent of lawyers on its site. (upcounsel.com)
- The BLS says that financial services jobs like banking are expected to grow 4% by 2030, about as fast as the national average. (wgu.edu)
- Our program is 100% engineered for your success. (online.uc.edu)
- 100% of the courses are offered online, and no campus visits are required — a big time-saver for you. (online.uc.edu)
External Links
How To
How can Lean Manufacturing be done?
Lean Manufacturing techniques are used to reduce waste while increasing efficiency by using structured methods. They were created in Japan by Toyota Motor Corporation during the 1980s. The main goal was to produce products at lower costs while maintaining quality. Lean manufacturing emphasizes removing unnecessary steps from the production process. It has five components: continuous improvement and pull systems; just-in time; continuous change; and kaizen (continuous innovation). The production of only what the customer needs without extra work is called pull systems. Continuous improvement is constantly improving upon existing processes. Just-in-time refers to when components and materials are delivered directly to the point where they are needed. Kaizen means continuous improvement, which is achieved by implementing small changes continuously. Finally, 5S stands for sort, set in order, shine, standardize, and sustain. These five elements are used together to ensure the best possible results.
Lean Production System
The lean production system is based on six key concepts:
-
Flow - focus on moving material and information as close to customers as possible;
-
Value stream mapping - break down each stage of a process into discrete tasks and create a flowchart of the entire process;
-
Five S's: Sort, Shine Standardize, Sustain, Set In Order, Shine and Shine
-
Kanban: Use visual signals such stickers, colored tape, or any other visual cues, to keep track your inventory.
-
Theory of Constraints - Identify bottlenecks in the process, and eliminate them using lean tools such kanban boards.
-
Just-intime - Order components and materials at your location right on the spot.
-
Continuous improvement: Make incremental improvements to the process instead of overhauling it completely.