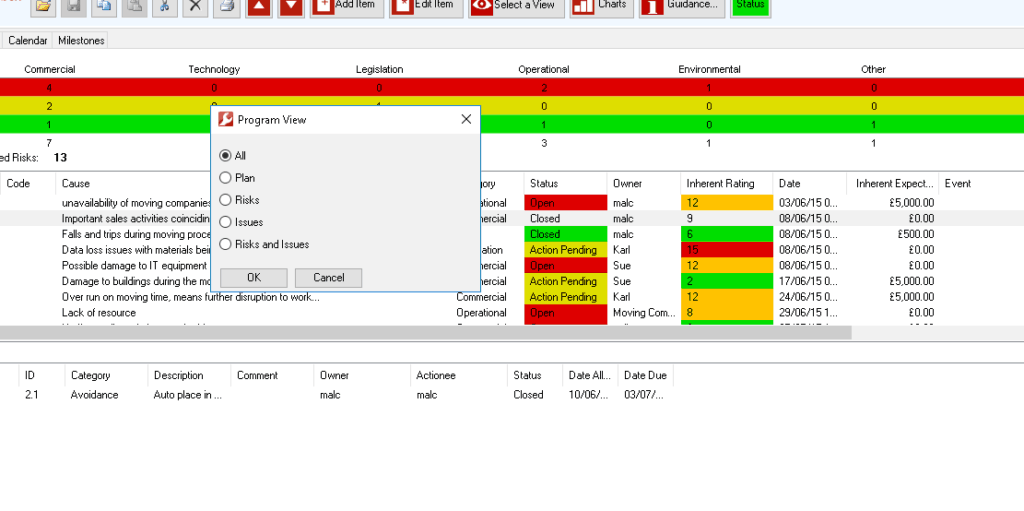
Engineering a building's structure is an important job. There are many types and levels of engineers involved in this industry. There are several types of engineers in the construction industry, including Civil engineers. These engineers develop construction plans from scratch and supervise the execution of these plans. They work in collaboration with other engineers and provide manual labor. Clients increasingly demand energy-efficient buildings. Engineers often have to offer alternative methods for generating power. Using solar energy, for example, is a common method for this process.
Civil engineers
A civil engineer is an individual who works on construction projects. They plan, design, construct, and test projects. They spend a lot of time at the site where they have to deal with multiple challenges and keep pace with progress. Their main goal is to create a structure that is safe and environmentally sound. Many people are interested in a career as a civil engineer.
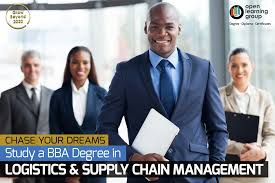
Structural engineers
From one project to the next, structural engineers play a variety of roles in construction. The role involves the analysis of the basic components of a building and liaising with other members of the project. Monitoring and inspecting work being done by contractors is another part of the job. This role may also involve the evaluation of the properties and conditions of the foundations. The computer-aided modeling (CAD) technology is also used by structural engineers to ensure that buildings are constructed correctly.
Electricians
The job of an electrical engineer on a construction site is crucial in ensuring maximum safety. They ensure that electrical appliances are safe for workers to use and that there are no bare connections. They also ensure that high risk areas are not accessible. The job requires a lot of time management and communication skills. Electrical engineers have to master all the technical and soft skills needed to keep a construction site safe. They must be aware of electrical safety codes.
Fire protection engineers
The chemistry and materials used in buildings are essential for fire protection engineers. They must also be familiar with the interactions between fire-fighting chemicals and suppression chemicals. They need to be able to communicate with the public as well as legal authorities. As a result, they have to know the proper procedures for presenting findings, creating court documents and studies. A Master of Science degree is desirable but not required. A doctorate in research is required for academia. There are many schools that offer fire protection engineering certification.
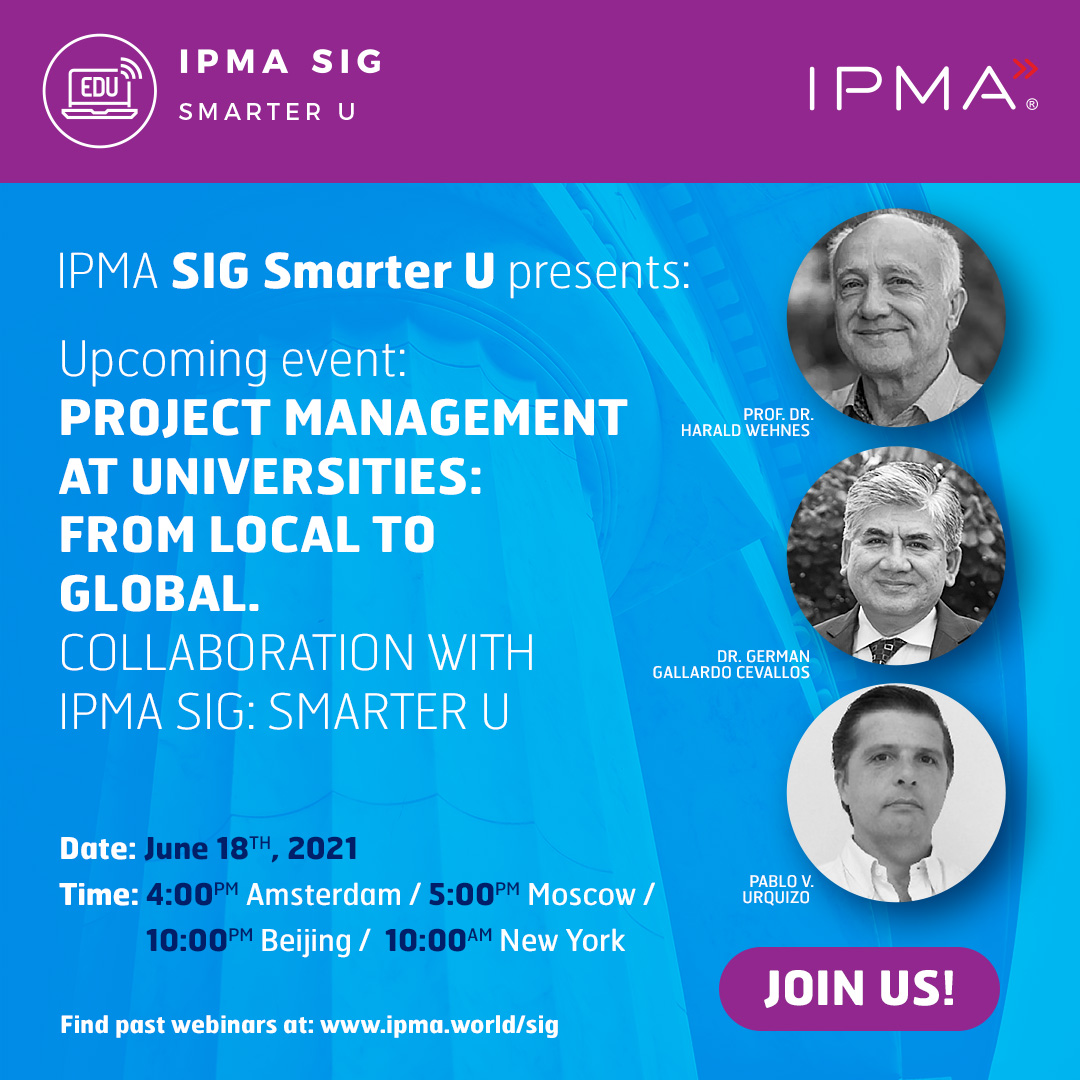
Environmental engineers
The construction industry is both the largest end-user of natural resources and the greatest source of pollution. The role of environmental engineers in the construction industry is to make it more sustainable and increase its performance. Environmental engineers can optimize construction sites while minimizing environmental impacts by using innovative design and life cycle assessments. The role of environmental engineers is to transform outdated practices into more sustainable ones. The future of the construction industry will be dependent on their expertise. Here are the main roles of environmental engineers.
FAQ
What are the four major functions of Management?
Management is responsible for organizing, managing, directing and controlling people, resources, and other activities. It includes creating policies and procedures, as well setting goals.
Management assists an organization in achieving its goals by providing direction, coordination and control, leadership, motivation, supervision and training, as well as evaluation.
These are the four major functions of management:
Planning - Planning refers to deciding what is needed.
Organizing - Organization involves deciding what should be done.
Direction - This is the art of getting people to follow your instructions.
Controlling - Controlling means ensuring that people carry out tasks according to plan.
What is the difference of leadership and management?
Leadership is all about influencing others. Management is about controlling others.
A leader inspires followers while a manager directs workers.
Leaders inspire people to achieve success. Managers keep their workers focused.
A leader develops people; a manager manages people.
Six Sigma is so beloved.
Six Sigma is easy to use and can lead to significant improvements. Six Sigma also gives companies a framework for measuring improvement and helps them focus on what is most important.
Statistics
- Our program is 100% engineered for your success. (online.uc.edu)
- Hire the top business lawyers and save up to 60% on legal fees (upcounsel.com)
- As of 2020, personal bankers or tellers make an average of $32,620 per year, according to the BLS. (wgu.edu)
- The profession is expected to grow 7% by 2028, a bit faster than the national average. (wgu.edu)
- UpCounsel accepts only the top 5 percent of lawyers on its site. (upcounsel.com)
External Links
How To
How do you do the Kaizen method?
Kaizen means continuous improvement. The term was coined in the 1950s at Toyota Motor Corporation and refers to the Japanese philosophy emphasizing constant improvement through small incremental changes. This is a collaborative process in which people work together to improve their processes continually.
Kaizen, a Lean Manufacturing method, is one of its most powerful. Employees responsible for the production line should identify potential problems in the manufacturing process and work together to resolve them. This way, the quality of products increases, and the cost decreases.
Kaizen is the idea that every worker should be aware of what is going on around them. Correct any errors immediately to avoid future problems. It is important that employees report any problems they see while on the job to their managers.
There are some basic principles that we follow when doing kaizen. We always start from the end product and move toward the beginning. For example, if we want to improve our factory, we first fix the machines that produce the final product. Next, we fix the machines which produce components. Then we fix the workers, who directly work with these machines.
This approach is called 'kaizen' because it focuses on improving everything steps by step. When we are done fixing the whole factory, we go back to the beginning and continue until we reach perfection.
You need to know how to measure the effectiveness of kaizen within your business. There are several ways to determine whether kaizen is working well. One method is to inspect the finished products for defects. Another way is to see how much productivity has increased since implementing kaizen.
If you want to find out if your kaizen is actually working, ask yourself why. It was because of the law, or simply because you wanted to save some money. Did you really believe that it would be a success factor?
Suppose you answered yes to any of these questions, congratulations! You are now ready to begin kaizen.