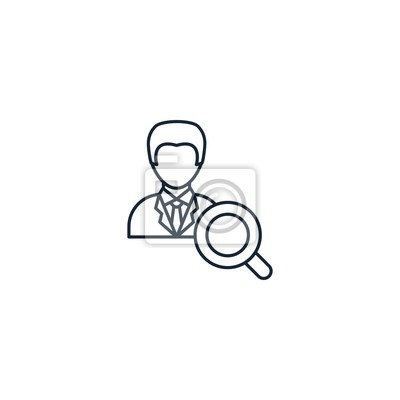
Process safety management aims to ensure that operating systems and processes are safe. This system is a legal requirement for major hazard facilities and must be updated at least every five years. The goal is to prevent potential incidents. These steps will help you get started with process management. These steps will ensure safety in your facilities and help to prevent accidents.
Process safety management is a disciplined framework for managing the integrity of operating systems and processes
The goal of process safety management (PSM) is to minimize the likelihood of incidents and improve productivity. It emphasizes the control of risks within the plant, and inherently safer machinery. It includes strict compliance to operating procedures and hazard assessments. It includes the training and maintenance of your plant, as well as process control. It is an essential element of a safety-conscious business.
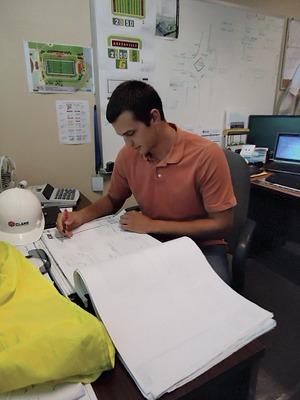
It must be kept current every 5 year
OSHA requires that the processes be reviewed and maintained regularly. This includes the creation of written procedures and safety information. This information must be available to all employees involved in the process. Written procedures and investigation reports must be kept for five years. Employees should have easy access to up-to-date process safety information. An employer may seek out safety risk management consulting to help them meet their requirements.
It is a legal requirement for major hazard facilities
For all major hazard areas, the process safety management system must be implemented. Employers are required to implement a process for safe and prompt evacuation of employees. Most cases, the plan will include a safety alarm to alert employees to evacuate. It should also contain emergency procedures to aid employees who are not physically able to evacuate the hazardous zone.
It helps to prevent incidents
A well-designed process management system for safety can enhance a company's safety performance and profitability. It can also improve the company's environmental responsibility. It also reduces the chance of accidents. These are four key areas for long-term success in a company. Here's a summary of the benefits of a process management system. It's a tool that prevents accidents and helps improve safety for employees and customers.
It can be time-consuming.
The process safety management of hazardous chemical facilities can be complex and time-consuming. OSHA doesn’t regulate safety management programs but it does require that all facilities have a written plan and adhere to 14 minimum standards. Some companies rely heavily on spreadsheets, forms and forms to collect information and compile risk analyses and other information. This is time-consuming, and there is a risk of human error.
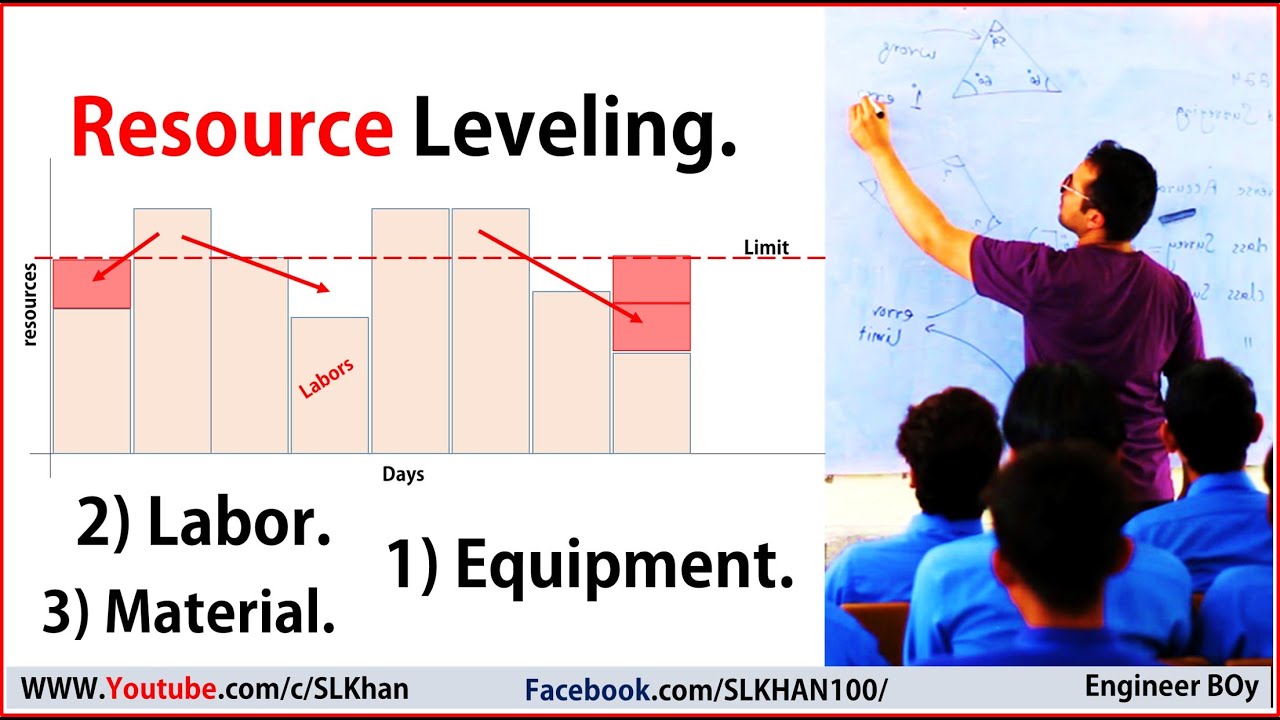
It requires employee participation
The Pennsylvania State University adopted a PSM program that includes an Employee Participation element. This element draws on employees' experience and knowledge to increase safety. This program outlines the various mechanisms that employees can participate and specifies the minimum requirements. All employees should be included in the safety management process. To avoid serious incidents, employee participation in PSM can be crucial. How can you make sure that everyone is involved in the program?
FAQ
What is the difference between a project and a program?
A project is temporary; a program is permanent.
A project has usually a specified goal and a time limit.
It is usually done by a group that reports back to another person.
A program is usually defined by a set or goals.
It is typically done by one person.
Why does it sometimes seem so hard to make good business decisions
Complex systems and many moving parts make up businesses. It is difficult for people in charge of businesses to manage multiple priorities simultaneously and also deal with uncertainty.
To make good decisions, you must understand how these factors affect the entire system.
To do this, you must think carefully about what each part of the system does and why. Next, consider how each piece interacts with the others.
It is also worth asking yourself if you have any unspoken assumptions about how you have been doing things. If you don't have any, it may be time to revisit them.
Asking for assistance from someone else is a good idea if you are still having trouble. They might see things differently than you and may have some insights that could help find a solution.
What are the five management steps?
The five stages of a business include planning, execution (monitoring), review, evaluation, and review.
Planning involves setting goals for the future. It involves setting goals and making plans.
Execution occurs when you actually carry out the plans. You need to make sure they're followed by everyone involved.
Monitoring allows you to monitor your progress towards achieving your goals. Monitoring should include regular reviews of performance against goals and budgets.
Each year, reviews are held at the end. They are a chance to see if everything went smoothly during the year. If not there are changes that can be made to improve the performance next year.
After each year's review, evaluation occurs. It helps identify which aspects worked well and which didn't. It provides feedback about how people perform.
How can we make our company culture successful?
A positive company culture creates a sense of belonging and respect in its people.
It's founded on three principal principles:
-
Everyone has something to contribute
-
Fair treatment of people is the goal
-
Respect is shared between individuals and groups
These values are reflected by the way people behave. They will show consideration and courtesy to others.
They will respect the opinions of others.
They will also encourage others to share their ideas and feelings.
In addition, the company culture encourages open communication and collaboration.
People are free to speak out without fear of reprisal.
They know that they will not be judged if they make mistakes, as long as the matter is dealt with honestly.
Finally, the company culture promotes integrity and honesty.
Everyone is aware that truth must be told.
Everyone understands that there are rules and regulations which apply to them.
No one is entitled to any special treatment or favors.
What are management concepts?
Management concepts are the principles and practices used by managers to manage people, resources. These include topics such as human resource policies and job descriptions, performance assessments, training programs and employee motivation.
What are some common mistakes managers make when managing people?
Managers can make their jobs more difficult than necessary.
They may not delegate enough responsibilities to staff and fail to give them adequate support.
In addition, many managers lack the communication skills required to motivate and lead their teams.
Managers set unrealistic expectations and make it difficult for their team.
Some managers may try to solve every problem themselves instead of delegating responsibility to others.
Statistics
- Your choice in Step 5 may very likely be the same or similar to the alternative you placed at the top of your list at the end of Step 4. (umassd.edu)
- Hire the top business lawyers and save up to 60% on legal fees (upcounsel.com)
- This field is expected to grow about 7% by 2028, a bit faster than the national average for job growth. (wgu.edu)
- UpCounsel accepts only the top 5 percent of lawyers on its site. (upcounsel.com)
- 100% of the courses are offered online, and no campus visits are required — a big time-saver for you. (online.uc.edu)
External Links
How To
How do you implement Quality Management Plans (QMPs)?
QMP (Quality Management Plan) is a system to improve products and services by implementing continuous improvement. It emphasizes on how to continuously measure, analyze, control, and improve processes, product/service, and customer satisfaction.
QMP is a method that ensures good business performance. QMP improves production, service delivery, as well as customer relations. QMPs should encompass all three components - Products and Services, as well as Processes. The QMP that only addresses one aspect of the process is called a Process QMP. QMP stands for Product/Service. QMP is also used to refer to QMPs that focus on customer relations.
When implementing a QMP, there are two main elements: Scope and Strategy. These are the following:
Scope: This describes the scope and duration for the QMP. If your organization wishes to implement a QMP lasting six months, the scope will determine the activities during the first six month.
Strategy: This describes the steps taken towards achieving the goals set forth in the scope.
A typical QMP consists of 5 phases: Planning, Design, Development, Implementation, and Maintenance. Below is a description of each phase:
Planning: In this stage, the objectives of the QMP are identified and prioritized. To understand the expectations and requirements of all stakeholders, the project is consulted. Next, you will need to identify the objectives and priorities. The strategy for achieving them is developed.
Design: The design stage involves the development of vision, mission strategies, tactics, and strategies that will allow for successful implementation. These strategies are put into action by developing detailed plans and procedures.
Development: Here, the team develops the resources and capabilities that will support the successful implementation.
Implementation: This refers to the actual implementation or the use of the strategies planned.
Maintenance: This is an ongoing procedure to keep the QMP in good condition over time.
Additional items must be included in QMP.
Stakeholder Engagement: It is crucial for the QMP to be a success. They should actively be involved during the planning and development, implementation, maintenance, and design stages of QMP.
Project Initiation: The initiation of any project requires a clear understanding of the problem statement and the solution. Also, the initiator should understand why they are doing it and what they expect.
Time Frame: It is important to consider the QMP's time frame. If you plan to implement the QMP for a short period, you can start with a simple version. You may need to upgrade if you plan on implementing the QMP for a long time.
Cost Estimation. Cost estimation is another crucial component of QMP. It is impossible to plan without knowing what you will spend. Before you start the QMP, it is important to estimate your costs.
QMPs are not only a document, but also a living document. This is the most important aspect of QMPs. It changes with the company. It should be reviewed regularly to ensure that it meets current needs.