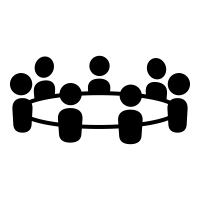
How can we define supply-chain management? Supply chain management describes a process that manages commerce. It encompasses the entire supply chain, from the raw materials and inventory in work-in-process to the fulfillment of orders. We will now discuss the different aspects of supply chain management. To better understand what they are, let's examine the four key components of a supply chain. These are the benefits of supply-chain management and how it can be beneficial to your company.
Product portfolio planning
Portfolio planning is a tool that helps companies develop new products and manage inventories to meet changing market needs. This includes monitoring the consumption of project resources. Proper financial management can boost cash flow and supplement current expenses. Planning new products is often a collaborative effort between multiple departments in a company. If there are miscommunications or disconnections, it can be difficult to get the plan right. To avoid this, it is important to keep lines of communication open and to check on targets regularly.
Organizations must think about their long-term goals and business strategy in order to effectively implement product portfolios. A company that aligns its current projects with its long-term goals can achieve higher sales, profits, and increased market share. Product portfolio planning helps companies determine which products are most profitable and offer the highest return on investment. It also helps them identify which products are redundant and which ones are cash cows.
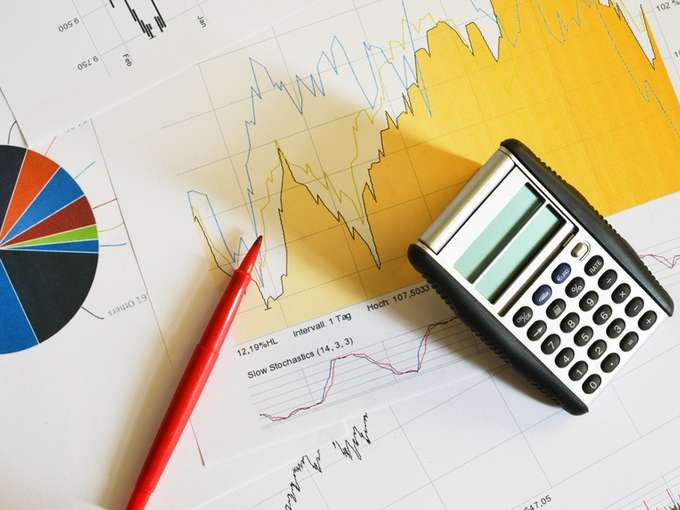
Distribution planning
Distribution planning, also known by distribution requirements planning (DRP), refers to a systematic process for determining how many of each good to produce and where they will be stored. This type of planning minimizes shortages and costs of ordering by considering how many products a certain region will require. This tool uses a tree-like structure that determines the supply source's gross requirements and how much inventory each item will require. A DRP tool can be used by manufacturers to optimize their key performance indicators in order determine which distribution plan is most profitable.
Distribution planning, an integral part supply chain management, involves a number sub-discipline practices to help make the process more effective. One such practice is just-in–time inventory. Distribution is essential for success, as there are many moving parts. It is crucial to have a strong distribution management strategy. This also requires real-time data. Here are some key components to a successful distribution strategy.
Planning for sales and operations
S&OP (sales & operations planning) is a process that's used in supply chain control to coordinate activities among business units and achieve profitability. S&OP can take place on a monthly basis, an annual basis, or for two years. It involves demand and supply planning, forecasting, and executive reviews. The goal is to create a better customer experience, and improve the bottom line. This process should not be limited to spreadsheets. It should be used by companies that have more than one location.
Regardless of the scale of the company, effective sales and operations planning will require strong leadership and a strong central figure. The goal is to foster cohesion between conflicting elements of the business, but a central figure must be involved to ensure that standards are met. The leader in sales should take part in the process. He or she should ensure that the process is conducted correctly.
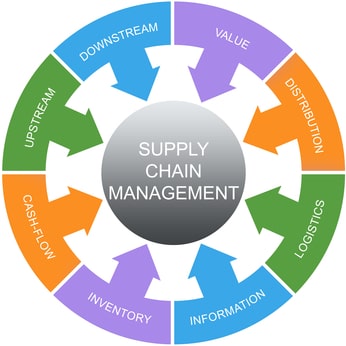
Planning for trade promotion
Trade Promotion Planning can be a crucial part of any company's success. Trade promotion refers to the marketing activity that a manufacturer does with a retailer. This could include promotions, coupons and discounts that increase demand from retailers. In the end, this will lead to higher sales. Here are the fundamental elements of successful trade promotion planning. These are the key elements to a successful trade promotion program:
Promotion planning refers to the management of special events, other than a forecast. This planning process involves calculating the effects of a promotion using causal techniques and projecting these into designated periods in the future. It's used to create marketing plans that can be used for both single and repeated events. Consensus demand planning involves combining various data sources to derive a consensus demand plan. This involves many activities such as safety stock planning and distribution planning.
FAQ
What are the three main management styles you can use?
There are three main management styles: participative, laissez-faire and authoritarian. Each style has strengths and flaws. Which style do YOU prefer? Why?
Authority - The leader is the one who sets the direction and expects everyone in the organization to follow it. This style is best when the organization has a large and stable workforce.
Laissez-faire - The leader allows each individual to decide for him/herself. This style works best when an organization is small and dynamic.
Participative - Leaders listen to all ideas and suggestions. This style works best in smaller organizations where everyone feels valued.
What is the difference between TQM and Six Sigma?
The major difference between the two tools for quality management is that six Sigma focuses on eliminating defect while total quality control (TQM), on improving processes and decreasing costs.
Six Sigma can be described as a strategy for continuous improvement. It emphasizes the elimination and improvement of defects using statistical methods, such as control charts, P-charts and Pareto analysis.
This method aims to reduce variation in product production. This is achieved by identifying and addressing the root causes of problems.
Total quality management refers to the monitoring and measurement of all aspects in an organization. It also includes the training of employees to improve performance.
It is frequently used as an approach to increasing productivity.
What are the five management methods?
The five stages of a business include planning, execution (monitoring), review, evaluation, and review.
Setting goals for the future is part of planning. It involves setting goals and making plans.
Execution occurs when you actually carry out the plans. They must be followed by all parties.
Monitoring is the process of evaluating your progress toward achieving your objectives. Regular reviews of performance against targets, budgets, and other goals should be part.
Reviews take place at the end of each year. They allow for an assessment of whether all went well throughout the year. If not, changes may be made to improve the performance next time around.
Evaluation takes place after the annual review. It helps identify which aspects worked well and which didn't. It provides feedback about how people perform.
Six Sigma is so popular.
Six Sigma is simple to implement and can yield significant results. It provides a framework that allows for improvement and helps companies concentrate on what really matters.
How does a manager develop his/her management skills?
By practicing good management skills at all times.
Managers need to monitor their subordinates' performance.
If you notice your subordinate isn't performing up to par, you must take action quickly.
You should be able to identify what needs improvement and how to improve things.
Statistics
- This field is expected to grow about 7% by 2028, a bit faster than the national average for job growth. (wgu.edu)
- UpCounsel accepts only the top 5 percent of lawyers on its site. (upcounsel.com)
- Our program is 100% engineered for your success. (online.uc.edu)
- 100% of the courses are offered online, and no campus visits are required — a big time-saver for you. (online.uc.edu)
- The average salary for financial advisors in 2021 is around $60,000 per year, with the top 10% of the profession making more than $111,000 per year. (wgu.edu)
External Links
How To
How does Lean Manufacturing work?
Lean Manufacturing uses structured methods to reduce waste, increase efficiency and reduce waste. They were developed in Japan by Toyota Motor Corporation (in the 1980s). The main goal was to produce products at lower costs while maintaining quality. Lean manufacturing seeks to eliminate unnecessary steps and activities in the production process. It has five components: continuous improvement and pull systems; just-in time; continuous change; and kaizen (continuous innovation). Pull systems are able to produce exactly what the customer requires without extra work. Continuous improvement means continuously improving on existing processes. Just-intime refers the time components and materials arrive at the exact place where they are needed. Kaizen stands for continuous improvement. Kaizen can be described as a process of making small improvements continuously. Last but not least, 5S is for sort. These five elements are combined to give you the best possible results.
Lean Production System
The lean production system is based on six key concepts:
-
Flow - The focus is on moving information and material as close as possible to customers.
-
Value stream mapping: This is a way to break down each stage into separate tasks and create a flowchart for the entire process.
-
Five S’s - Sorted, In Order. Shine. Standardize. And Sustain.
-
Kanban - visual cues such as stickers or colored tape can be used to track inventory.
-
Theory of constraints - identify bottlenecks in the process and eliminate them using lean tools like kanban boards;
-
Just-in time - Get components and materials delivered right at the point of usage;
-
Continuous improvement - make incremental improvements to the process rather than overhauling it all at once.