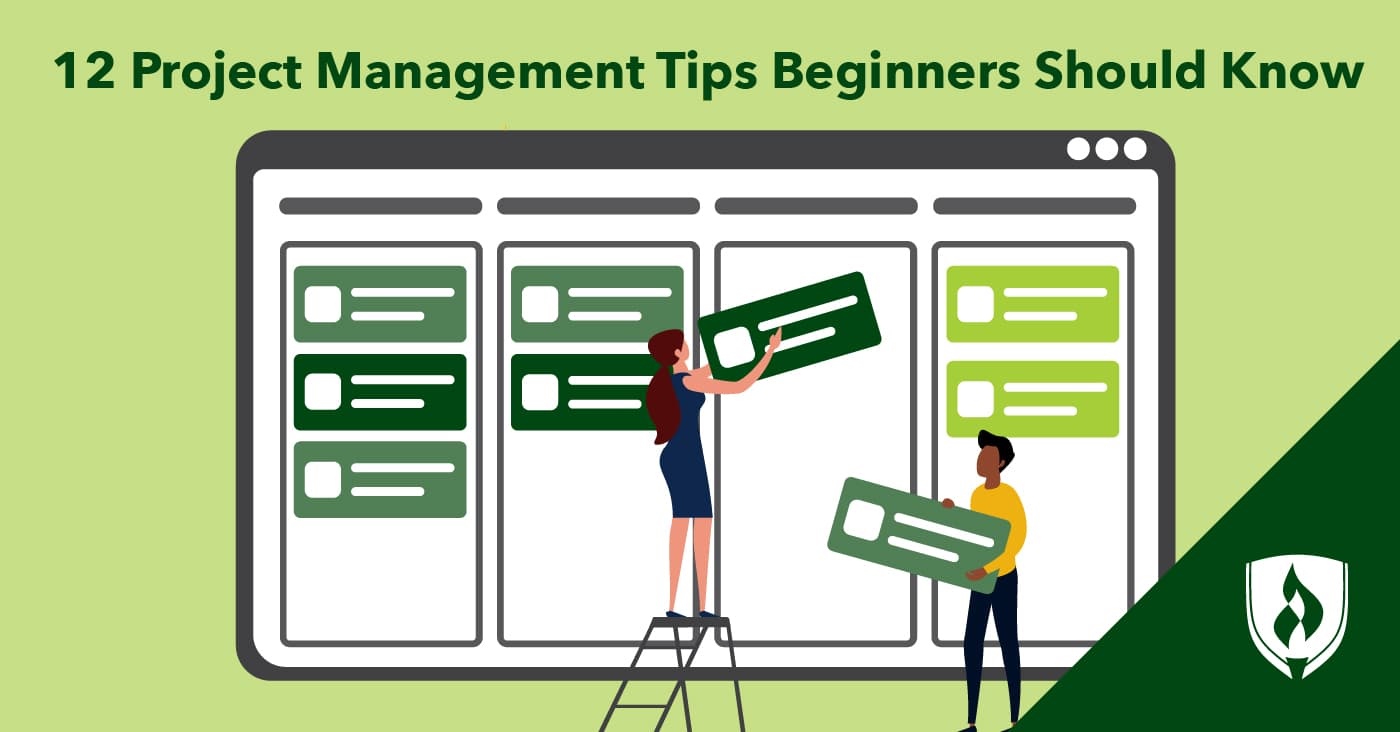
Submit your webinar idea if you would like to host a webinar on a specific topic. Participation in CMAA webinars is free and you will earn one CCM Renewal Point and one Professional Development Hour. Submit your idea here for a webinar on construction.
Send your ideas for a webinar about the business of construction
There are many different ways to promote your webinar. The best way to promote your webinar is to create a landing page. A landing page doesn't need to be complicated. Simple pages can work. You should also create blog posts to promote your webinar. You can increase your webinar's visibility by sharing it with others.
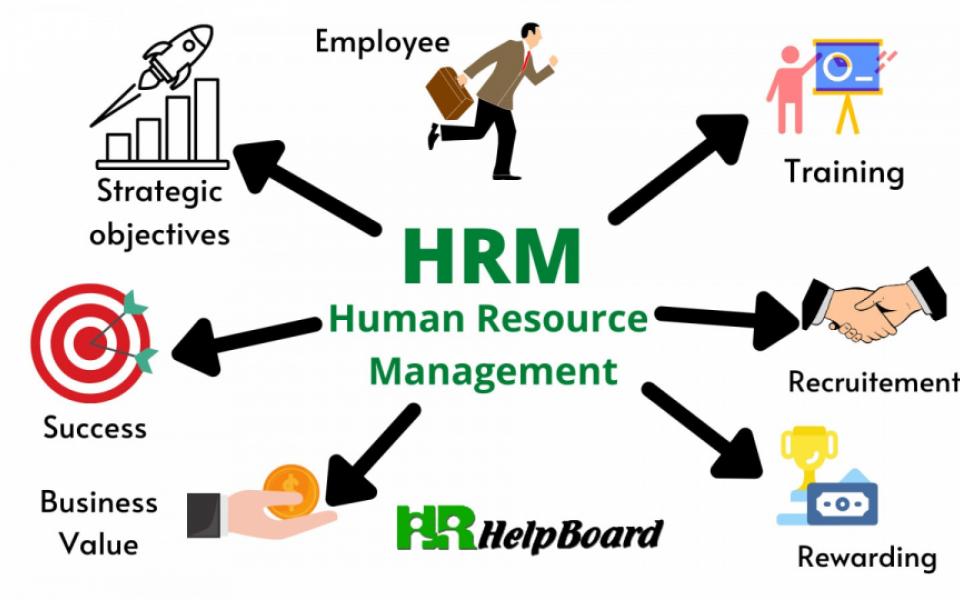
CMAA webinars offer 1 CCM Renewal Point (RP) and 1 Professional Development Hour (PDH)
CMAA webinars can be accessed worldwide by CMs. Each webinar offers either 1 CCM Renewal point (RP) or 1 Professional Development Hour (PDH). PDHs are for professional development and continuing education credits. RMs can also be used to renew your CCM credential. This credential is valid two years.
The CMAA Southern Nevada Chapter offers professional development opportunities for construction managers, including monthly breakfast meetings, educational events, and CCM certification. CMAA offers training and professional education for construction managers. Professional development is available for anyone looking to improve their skills or gain new insights.
Benefits of attending a webinar
A webinar is an excellent way to increase your sales leads, and improve customer service. The webinar can be delivered in many formats: a single speaker, panel discussions or a moderator who presents multiple speakers. A webinar that succeeds will communicate a strong message to the audience and be different from other webinars.
Webinars can be viewed at any time that is convenient for the participants. The presenter can prerecord and then upload the webinar at a convenient time. The entire experience is highly customizable. Webinars can also be accessed geographically so that anyone can participate.
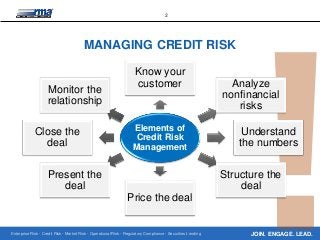
Webinars offer a chance to make connections and expand your network. Webinars allow participants to ask questions, and receive feedback. A webinar can also be used to facilitate thought leadership discussions or training on the latest trends in the industry. Webinars are a great way to reach a large audience in a short amount of time.
FAQ
What are the 5 management processes?
The five stages of any business are planning, execution, monitoring, review, and evaluation.
Setting goals for the future requires planning. It includes defining what you want to achieve and how you plan to do it.
Execution takes place when you actually implement the plans. Everyone involved must follow them.
Monitoring is the act of monitoring your progress towards achieving your targets. This should involve regular reviews of performance against targets and budgets.
At the end of every year, reviews take place. They give you an opportunity to review the year and assess how it went. If not, it is possible to make improvements for next year.
After the annual review, evaluation takes place. It helps identify which aspects worked well and which didn't. It also gives feedback on how well people did.
Why does it sometimes seem so difficult to make good business decisions?
Businesses are complex systems, and they have many moving parts. It is difficult for people in charge of businesses to manage multiple priorities simultaneously and also deal with uncertainty.
Understanding the impact of these factors on the system is crucial to making sound decisions.
You need to be clear about the roles and responsibilities of each system. You then need to consider how those individual pieces interact with each other.
You should also ask yourself if there are any hidden assumptions behind how you've been doing things. If not, you might want to revisit them.
You can always ask someone for help if you still have questions after all of this. You might find their perspective is different from yours and they may have insight that can help you find the solution.
What is the main difference between Six Sigma Six Sigma TQM and Six Sigma Six Sigma?
The main difference between these two quality management tools is that six sigma focuses on eliminating defects while total quality management (TQM) focuses on improving processes and reducing costs.
Six Sigma stands for continuous improvement. It emphasizes the elimination of defects by using statistical methods such as control charts, p-charts, and Pareto analysis.
This method has the goal to reduce variation of product output. This is done by identifying and correcting the root causes of problems.
Total quality management includes monitoring and measuring all aspects of an organization's performance. Training employees is also part of total quality management.
It is frequently used as an approach to increasing productivity.
Statistics
- Your choice in Step 5 may very likely be the same or similar to the alternative you placed at the top of your list at the end of Step 4. (umassd.edu)
- 100% of the courses are offered online, and no campus visits are required — a big time-saver for you. (online.uc.edu)
- This field is expected to grow about 7% by 2028, a bit faster than the national average for job growth. (wgu.edu)
- As of 2020, personal bankers or tellers make an average of $32,620 per year, according to the BLS. (wgu.edu)
- UpCounsel accepts only the top 5 percent of lawyers on its site. (upcounsel.com)
External Links
How To
How do I do the Kaizen Method?
Kaizen means continuous improvement. The term was coined in the 1950s at Toyota Motor Corporation and refers to the Japanese philosophy emphasizing constant improvement through small incremental changes. It's a team effort to continuously improve processes.
Kaizen is one method that Lean Manufacturing uses to its greatest advantage. The concept involves employees responsible for manufacturing identifying problems and trying to fix them before they become serious issues. This way, the quality of products increases, and the cost decreases.
Kaizen is the idea that every worker should be aware of what is going on around them. To prevent problems from happening, any problem should be addressed immediately. It is important that employees report any problems they see while on the job to their managers.
Kaizen is based on a few principles. Start with the end product, and then move to the beginning. If we want to improve our factory for example, we start by fixing the machines that make the final product. First, we fix machines that produce components. Next, we fix machines that produce raw material. Then, we fix those who work directly with the machines.
This method is known as kaizen because it focuses upon improving every aspect of the process step by step. We finish fixing the factory and then go back to the beginning. This continues until we achieve perfection.
How to measure kaizen's effectiveness in your business is essential to implement it. There are many ways you can determine if kaizen has been implemented well. Another way to determine if kaizen is working well is to look at the quality of the products. Another method is to determine how much productivity has improved since the implementation of kaizen.
Another way to know whether kaizen is working is to ask yourself why did you decide to implement kaizen. You were trying to save money or obey the law? Did you really think that it would help you achieve success?
Let's say you answered yes or all of these questions. Congratulations! You are now ready to begin kaizen.