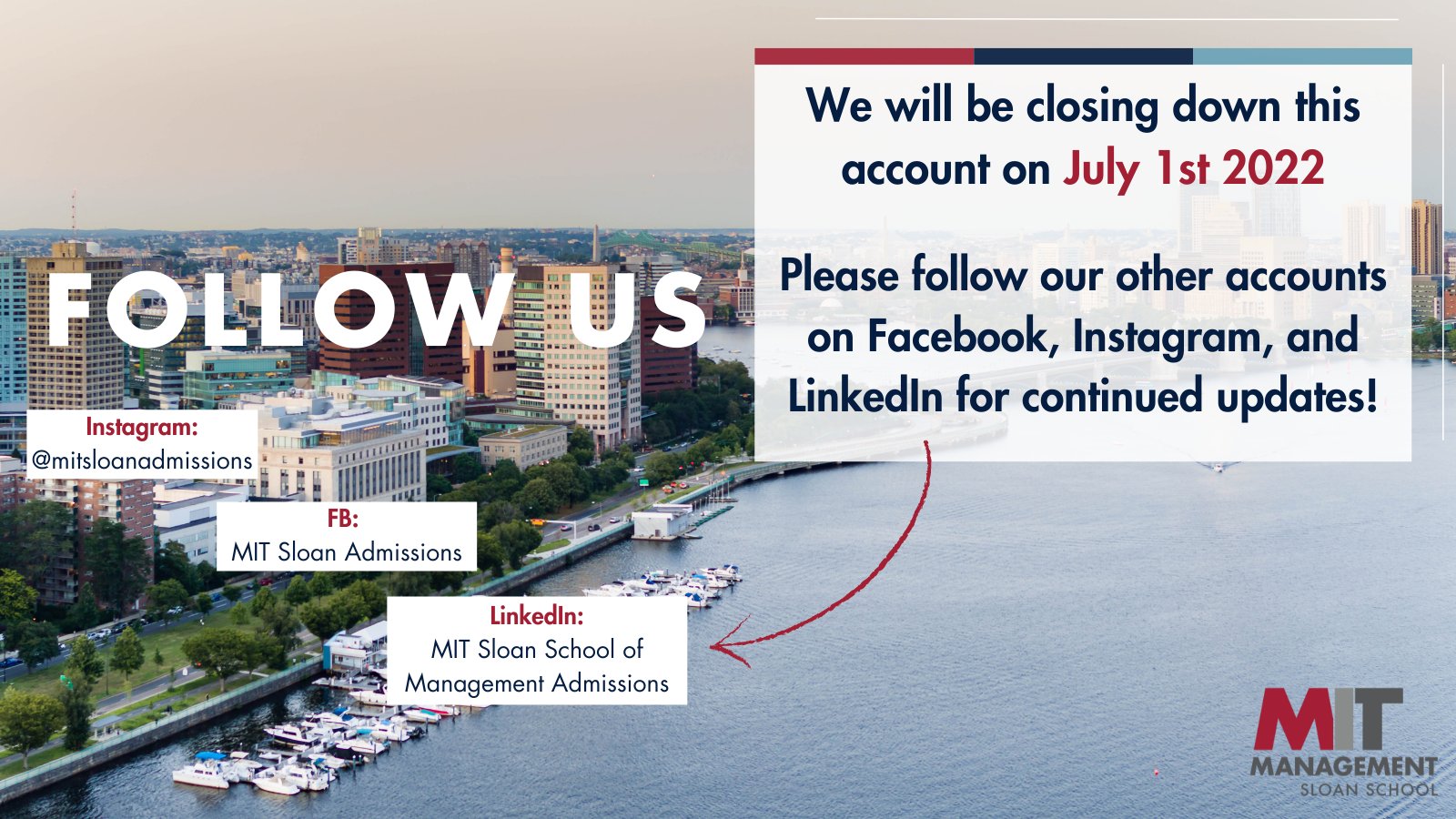
You must be able to manage projects effectively and have the right skills. To meet your project's goals, you must stay on budget and on schedule. Here are some tips for project management to help you reach your goals. Keep track of all your team members' tasks, deadlines, and create a to do list. Finally, set SMART goals. You should also learn how communicate effectively and with stakeholders.
Keeping track of team members' tasks and deadlines
A key part of project management involves keeping track the tasks of your team members and the deadlines to complete them. It helps team members stay on track, and help them achieve a common goal. It helps the team better manage their workday. To accomplish this, the team should first determine the main objective for the project, and then create a tasklist. This list should contain the tasks that will contribute to the project's main objective, the time each task will take, as well as the deadline. These tasks should then be prioritized according to their importance. The highest priority tasks should be at the top.
It is easy to use project management software to help you divide your projects into tasks, assign them to people, and create deadlines. The software keeps track of time spent on each task as well as the progress made. You can also create colorful labels that describe the current status of a task.
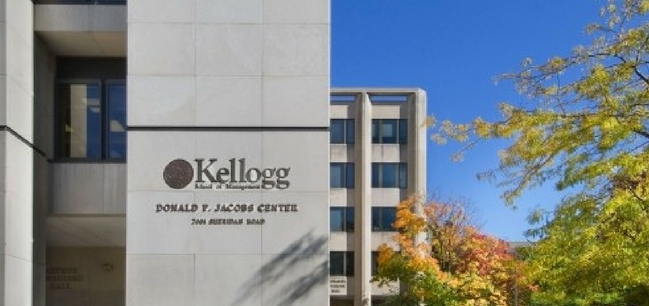
Creating a to-do list
Creating a to-do list is a good way to keep track of your tasks and prioritize your projects. You should list deadlines, names and goals of the team members. It's also a good idea for team members to see the list to hold them accountable for their work.
Before you begin creating your to-do lists, choose the best medium for your tasks. Try to write specific tasks, instead of general ones. You don't want to write vague, non-actionable tasks. For example, you could write "write an outline for a blog post". Give each task a rating such as "important," or "needs it done today"
Setting SMART goals
SMART Goals are measurable targets. They are realizable by setting out the final outcome and a time frame. Having a time frame for goal achievement is vital because it will keep people on track and motivated. In addition, SMART goals are easily understood by others, especially if you use clear language.
Project managers should set SMART goals as they will provide a benchmark for success. They should be specific and relate to the overall organizational goal. They should also have a clear ending marker.
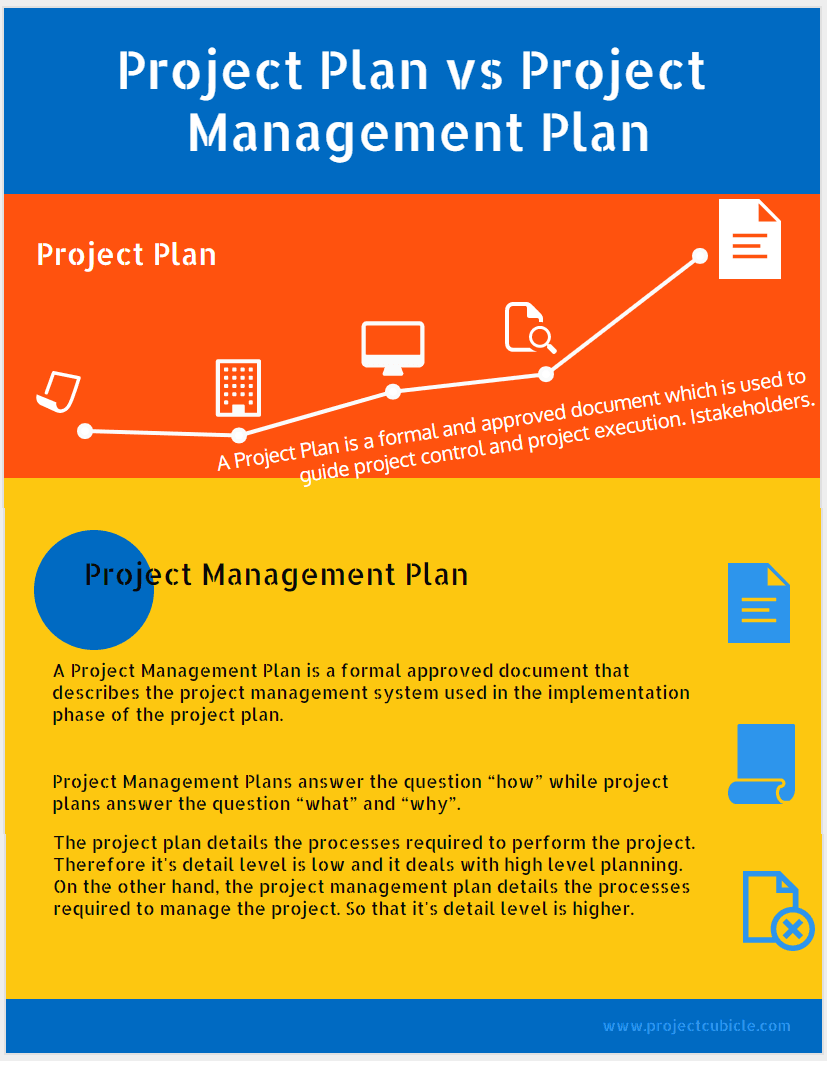
Managing risk
Project risk management is the process that minimizes the risks associated with a given project. This helps to ensure that the project meets its goals and is completed within the budget and time allowed. This is crucial to the success and sustainability of any project. There are many ways to reduce risk. These methods include risk analysis, risk planning, risk communication, and risk mitigation.
In the risk analysis process, you need to determine the probability of risk occurring and how it could affect the project. Consider the possible impact of a potential risk on the project's goals, budget, deliverables, and other factors. You will then need to create a response plan. This plan should not be an immediate action item, but rather a series of steps that will be taken if a risk occurs.
FAQ
How do we create a company culture that is productive?
A culture of respect and value within a company is key to a productive culture.
It's founded on three principal principles:
-
Everybody has something of value to share
-
Fair treatment of people is the goal
-
People and groups should respect each other.
These values are reflected by the way people behave. For example, they will treat others with courtesy and consideration.
They will listen to other people's opinions respectfully.
They will also encourage others to share their ideas and feelings.
The company culture promotes collaboration and open communication.
People feel safe to voice their opinions without fear of reprisal.
They know that they will not be judged if they make mistakes, as long as the matter is dealt with honestly.
Finally, the company culture promotes integrity and honesty.
Everybody knows they have to tell the truth.
Everyone understands that there are rules and regulations which apply to them.
No one is entitled to any special treatment or favors.
How does a manager learn to manage?
Through demonstrating good management skills at every opportunity
Managers must constantly monitor the performance of their subordinates.
It is important to take immediate action if your subordinate doesn't perform as expected.
You should be able to identify what needs improvement and how to improve things.
What is the best way to motivate your employees as a manager?
Motivation can be defined as the desire to achieve success.
Engaging in something fun can be a great way to get motivated.
Another way to get motivated is to see yourself as a contributor to the success of the company.
For example, if your goal is to become a physician, you will probably find it more motivational to see patients rather than to read a lot of medicine books.
A different type of motivation comes directly from the inside.
You may feel strongly that you are responsible to help others.
You may even find it enjoyable to work hard.
Ask yourself why you aren't feeling motivated.
Next, think of ways you can improve your motivation.
What's the difference between Six Sigma and TQM?
The key difference between the two quality management tools is that while six-sigma focuses its efforts on eliminating defects, total quality management (TQM), focuses more on improving processes and reducing cost.
Six Sigma stands for continuous improvement. This method emphasizes eliminating defects using statistical methods such p-charts, control charts, and Pareto analysis.
This method aims to reduce variation in product production. This is achieved by identifying and addressing the root causes of problems.
Total Quality Management involves monitoring and measuring every aspect of the organization. Training employees is also part of total quality management.
It is commonly used as a strategy for increasing productivity.
What is Kaizen?
Kaizen, a Japanese term that means "continuous improvement," is a philosophy that encourages employees and other workers to continuously improve their work environment.
Kaizen is built on the belief that everyone should be able do their jobs well.
What are management concepts, you ask?
Management Concepts are the management principles and practices that managers use in managing people and resources. These topics include job descriptions, performance evaluations and training programs. They also cover human resource policies, job description, job descriptions, job descriptions, employee motivation, compensation systems, organizational structures, and many other topics.
Statistics
- UpCounsel accepts only the top 5 percent of lawyers on its site. (upcounsel.com)
- The average salary for financial advisors in 2021 is around $60,000 per year, with the top 10% of the profession making more than $111,000 per year. (wgu.edu)
- Your choice in Step 5 may very likely be the same or similar to the alternative you placed at the top of your list at the end of Step 4. (umassd.edu)
- The BLS says that financial services jobs like banking are expected to grow 4% by 2030, about as fast as the national average. (wgu.edu)
- 100% of the courses are offered online, and no campus visits are required — a big time-saver for you. (online.uc.edu)
External Links
How To
How can Lean Manufacturing be done?
Lean Manufacturing methods are used to reduce waste through structured processes. They were created in Japan by Toyota Motor Corporation during the 1980s. The primary goal was to make products with lower costs and maintain high quality. Lean manufacturing is about eliminating redundant steps and activities from the manufacturing process. It includes five main elements: pull systems (continuous improvement), continuous improvement (just-in-time), kaizen (5S), and continuous change (continuous changes). Pull systems are able to produce exactly what the customer requires without extra work. Continuous improvement refers to continuously improving existing processes. Just-in time refers to components and materials being delivered right at the place they are needed. Kaizen means continuous improvement, which is achieved by implementing small changes continuously. The 5S acronym stands for sort in order, shine standardize and maintain. These five elements are combined to give you the best possible results.
The Lean Production System
Six key concepts are the basis of lean production:
-
Flow - focuses on moving information and materials as close to customers as possible.
-
Value stream mapping - break down each stage of a process into discrete tasks and create a flowchart of the entire process;
-
Five S's, Sort, Set in Order, Shine. Standardize. and Sustain.
-
Kanban: Use visual signals such stickers, colored tape, or any other visual cues, to keep track your inventory.
-
Theory of constraints - identify bottlenecks in the process and eliminate them using lean tools like kanban boards;
-
Just-in Time - Send components and material directly to the point-of-use;
-
Continuous improvement - Make incremental improvements rather than overhauling the entire process.