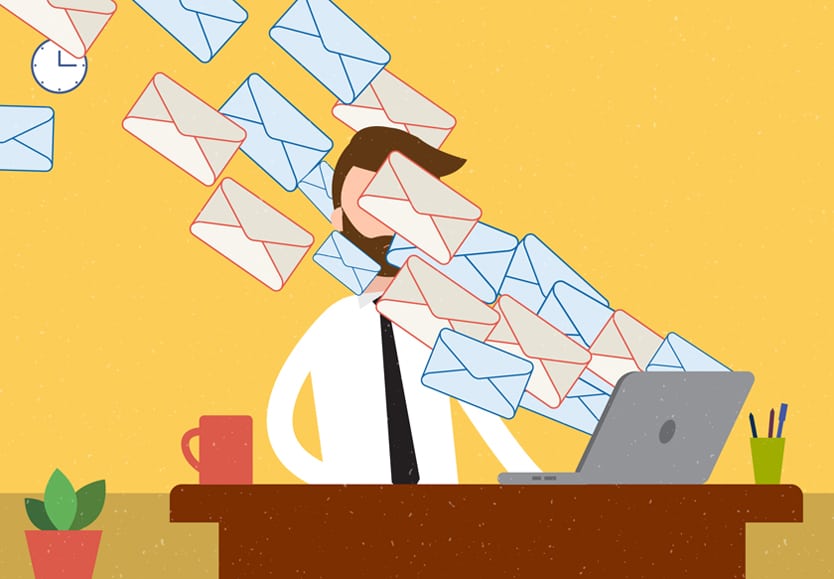
A company must follow 14 elements in order be considered as a PSM program. These elements include process hazard analyses and permissible exposure limits. These requirements are vital for the effective operation of a PSM program. A PSM program that complies with these requirements will be considered compliant. These elements are described and illustrated in the following sections.
Analyses of Process Hazards
A process hazards analysis is an important component of safety management programs. It helps to identify possible hazards and determine the consequences of failure. This analysis must be done with a group of people who are familiar with the process. It will review the site and include past incidents as well as human factors. Once the analysis is complete, it must be updated at least every five years. Hazard analysis must be used as part of safety management systems.
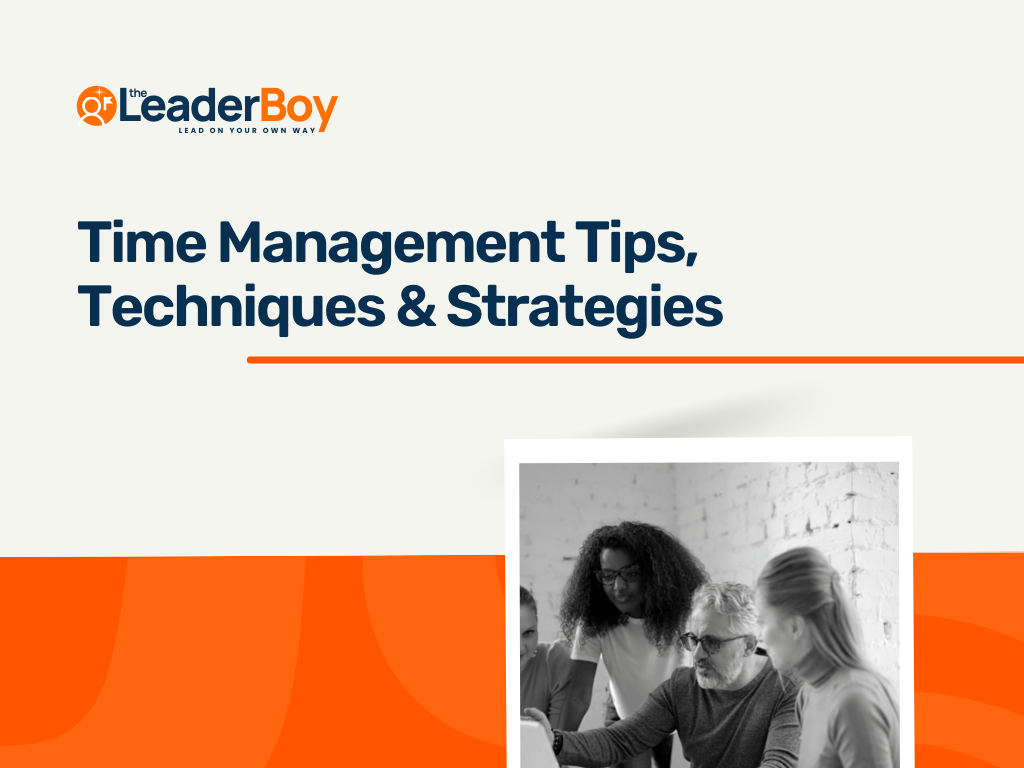
Permissible exposure limits
The OSHA Process Safety Management standard is a set of standards for processes that involve chemicals, gases, or liquids that are classified as hazardous. The standard applies only to businesses that manufacture or process hazardous chemicals. It does NOT apply to hydrocarbon fuels solely used at work, to retail or to oil and gas well-drilling. Similar to the remote or otherwise unoccupied facilities, it is not applicable.
Physical data
PSM is the process for analyzing and controlling hazardous materials and products. This entails understanding how to safely handle, transport, and store hazardous substances. This will result in less product waste and fewer workplace injuries. It helps make decision-making easier and ensures safety and health for employees. PSM is an essential part of a safe workplace. PSM can also help organizations prevent health emergencies and lower costs.
Corrosivity data
The PSM standard specifies requirements for the handling and storage of chemicals and other substances that can cause damage to buildings and equipment. The PSM requires periodic compliance audits and includes requirements for emergency plans and permit system. PSM-compliant work environments will prevent injuries and damage, regardless of whether hazardous substances were used in the production processes.
Thermal stability data
OSHA established a standard to collect and report PSM thermal stability data. The program will ensure that researchers are aware of possible hazards and minimize the effects of accidental release. It will be regularly reviewed and updated to meet the needs of new research projects. It will be available to all employees. The PSM program provides information on toxicity and reactivity as well as physical properties.
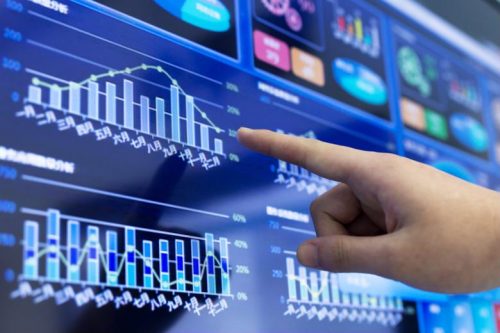
Employee participation clause
Process Safety Management (PSM) is a systematic analytical approach to the prevention of process accidents caused by highly hazardous chemicals (HHC). It is an important step to improving safety in process operations and should be implemented at all levels of the company, including production and maintenance departments. It contains 14 components that should be implemented. These include employee participation clauses. Below are some examples of these elements, along with their requirements.
FAQ
What is Kaizen?
Kaizen is a Japanese term for "continuous improvement." It encourages employees constantly to look for ways that they can improve their work environment.
Kaizen is a belief that everyone should have the ability to do their job well.
What are the 4 major functions of management
Management is responsible to plan, organize, direct, and control people and resources. This includes setting goals, developing policies and procedures, and creating procedures.
Management aids an organization in reaching its goals by providing direction and coordination, control, leadership motivation, supervision, training, evaluation, and leadership.
Management has four primary functions:
Planning - Planning involves determining what needs to be done.
Organizing - Organizing involves deciding how things should be done.
Directing - Directing is when you get people to do what you ask.
Controlling: Controlling refers to making sure that people do what they are supposed to.
What are the main management skills?
Managerial skills are crucial for every business owner, regardless of whether they run a small store in their locality or a large corporation. They are the ability to manage people and finances, space, money, and other factors.
You will need management skills to set goals and objectives, plan strategies, motivate employees, resolve problems, create policies and procedures, and manage change.
As you can see, there are many managerial responsibilities!
What is the meaning of "project management?"
This refers to managing all activities that are involved in a project's execution.
These include planning the scope and identifying the needs, creating the budget, organizing the team, scheduling the work and monitoring progress. Finally, we close down the project.
Statistics
- Hire the top business lawyers and save up to 60% on legal fees (upcounsel.com)
- As of 2020, personal bankers or tellers make an average of $32,620 per year, according to the BLS. (wgu.edu)
- Our program is 100% engineered for your success. (online.uc.edu)
- UpCounsel accepts only the top 5 percent of lawyers on its site. (upcounsel.com)
- The profession is expected to grow 7% by 2028, a bit faster than the national average. (wgu.edu)
External Links
How To
How can Lean Manufacturing be done?
Lean Manufacturing is a method to reduce waste and increase efficiency using structured methods. They were created in Japan by Toyota Motor Corporation during the 1980s. The main goal was to produce products at lower costs while maintaining quality. Lean manufacturing eliminates unnecessary steps and activities from a production process. It is composed of five fundamental elements: continuous improvement; pull systems, continuous improvements, just-in–time, kaizen, continuous change, and 5S. Pull systems are able to produce exactly what the customer requires without extra work. Continuous improvement means continuously improving on existing processes. Just-intime refers the time components and materials arrive at the exact place where they are needed. Kaizen refers to continuous improvement. It is achieved through small changes that are made continuously. Five-S stands for sort. It is also the acronym for shine, standardize (standardize), and sustain. These five elements can be combined to achieve the best possible results.
Lean Production System
Six key concepts underlie the lean production system.
-
Flow - focuses on moving information and materials as close to customers as possible.
-
Value stream mapping is the ability to divide a process into smaller tasks, and then create a flowchart that shows the entire process.
-
Five S’s - Sorted, In Order. Shine. Standardize. And Sustain.
-
Kanban: Use visual signals such stickers, colored tape, or any other visual cues, to keep track your inventory.
-
Theory of constraints - identify bottlenecks during the process and eliminate them with lean tools like Kanban boards.
-
Just-in-time - deliver components and materials directly to the point of use;
-
Continuous improvement - make incremental improvements to the process rather than overhauling it all at once.