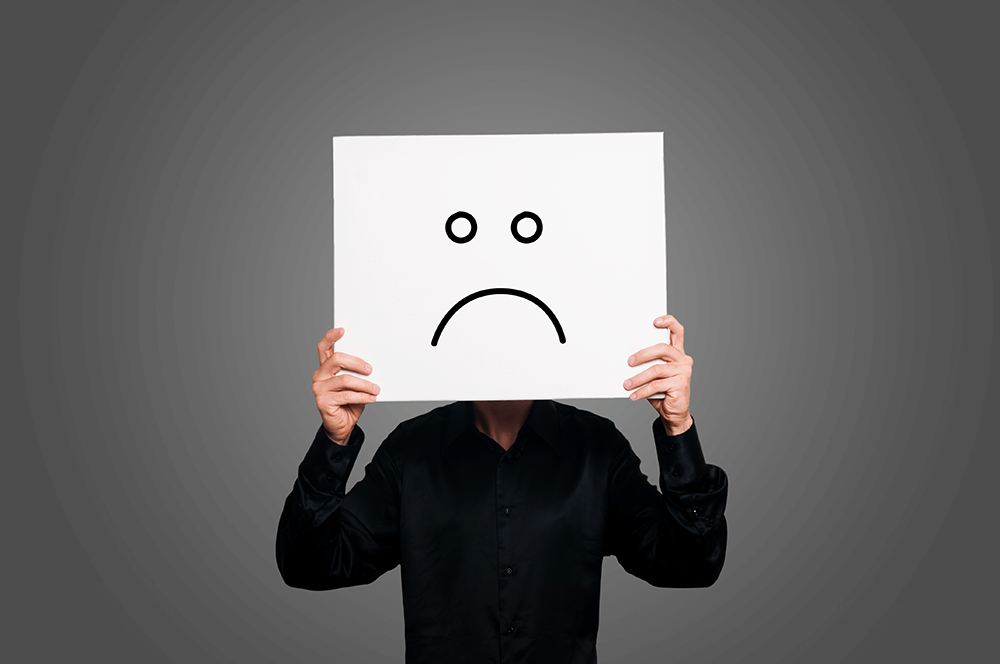
An essential part of project management is the identification and tracking of issues. This allows you to keep track of the progress of the project and keep everyone informed. You can keep track of issues using a log, a spreadsheet or another tool.
Issues are created by a range of factors, from staffing shortages to technical failures. These issues can be high- or low-priority and affect the success or failure of a project. If they are ignored, they can create major problems. These issues can be tracked and managed with issue management techniques.
To manage problems, you need a strategy and a plan. You may decide to try multiple avenues of action simultaneously. A dashboard for tracking issues might be a good idea to keep everyone updated on their status. But, it is important not to confuse issues and risks. It is crucial to know the difference.
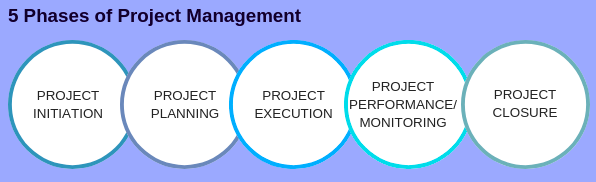
Issues can be found at any level of the organization. One example is if a team member isn't skilled enough, you might have to search for another person. There may be issues that prevent you from moving on to the next phase or reaching your project's objectives. A project can get stalled if an issue isn't addressed. Problem management can help you to identify and fix the issue, while minimising disruptions to the project.
Although issues can be identified at all levels, it is important to ensure that information is easily accessible to the people who require it. This includes both those who must report on the issue as well as others who may be interested in how it impacts the project. To track issues for projects that are less complicated than others, you may want to use a simple spreadsheet.
First, identify the problem. Sometimes, it is easy to identify problems by looking at the smallest details. For instance, you may notice that a particular staff member has been hospitalized for two weeks. It is important to follow up any issue you have identified in your issue tracker. You can also save the issue log to be used later.
You can also find opportunities in the face of problems. If a member of your team is suffering from a medical emergency, it may be possible to hire another member. Sometimes, the problem can be solved by someone else. It can help you spot potential issues before they become major problems.
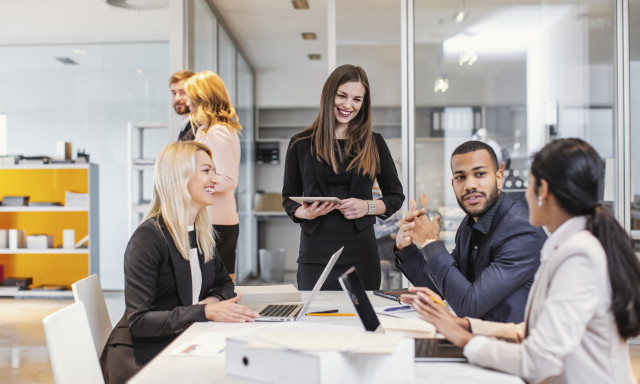
You can also refer to issue management as information technology service management, project management, or even information technology issue management. The key to project success is issue management, no matter the name. This involves tracking and identifying issues, assessing their impact, and creating a plan to address them. It is important that this process is tied to project governance.
You have the option of keeping track of issues using a spreadsheet, an issue log or another project management tool. In general, it is important to keep the issue log current with status reports as well as resolution comments and actions. Assign members of your team to the issues if you are able. You should also include a detailed resolution plan in your log.
FAQ
What is TQM, exactly?
The quality movement was born during the industrial revolution when manufacturing companies realized they could not compete on price alone. They had to improve efficiency and quality if they were to remain competitive.
Management realized the need to improve and created Total Quality Management, which focused on improving all aspects within an organization's performance. It included continuous improvement and employee involvement as well as customer satisfaction.
What can a manager do to improve his/her management skillset?
It is important to have good management skills.
Managers must continuously monitor the performance levels of their subordinates.
If you notice your subordinate isn't performing up to par, you must take action quickly.
It is essential to know what areas need to be improved and how to do it.
What are the main management skills?
Management skills are essential for any business owner, whether they're running a small local store or an international corporation. These include the ability and willingness to manage people, finances as well resources, time and space.
Managerial skills are required when setting goals and objectives and planning strategies, leading employees, motivating them, solving problems, creating policies, procedures, or managing change.
You can see that there are many managerial duties.
What are the main four functions of management
Management is responsible of planning, organizing, leading, and controlling people as well as resources. It includes the development of policies and procedures as well as setting goals.
Management assists an organization in achieving its goals by providing direction, coordination and control, leadership, motivation, supervision and training, as well as evaluation.
The four main functions of management are:
Planning - This is the process of deciding what should be done.
Organizing is the act of deciding how things should go.
Directing – This means to get people to follow directions.
Controlling: Controlling refers to making sure that people do what they are supposed to.
How can a manager motivate employees?
Motivation is the desire for success.
It is possible to be motivated by doing something you enjoy.
You can also feel motivated by making a positive contribution to the success in the organization.
If you are a doctor and want to be one, it will likely be more rewarding to see patients than to read medical books every day.
Another type of motivation comes from within.
You might feel a strong sense for responsibility and want to help others.
Maybe you like working hard.
Ask yourself why you feel so motivated.
Then, consider ways you could improve your motivation.
What role does a manager play in a company?
Different industries have different roles for managers.
Managers generally oversee the day-today operations of a business.
He/she ensures that the company meets its financial obligations and produces goods or services that customers want.
He/she is responsible for ensuring that employees comply with all regulations and follow quality standards.
He/she oversees marketing campaigns and plans new products.
Statistics
- 100% of the courses are offered online, and no campus visits are required — a big time-saver for you. (online.uc.edu)
- UpCounsel accepts only the top 5 percent of lawyers on its site. (upcounsel.com)
- As of 2020, personal bankers or tellers make an average of $32,620 per year, according to the BLS. (wgu.edu)
- The profession is expected to grow 7% by 2028, a bit faster than the national average. (wgu.edu)
- This field is expected to grow about 7% by 2028, a bit faster than the national average for job growth. (wgu.edu)
External Links
How To
How do I do the Kaizen Method?
Kaizen means continuous improvement. The Japanese philosophy emphasizes small, incremental improvements to achieve continuous improvement. This term was created by Toyota Motor Corporation in 1950. It's a process where people work together to improve their processes continuously.
Kaizen is one of the most effective methods used in Lean Manufacturing. Employees responsible for the production line should identify potential problems in the manufacturing process and work together to resolve them. This way, the quality of products increases, and the cost decreases.
Kaizen is an approach to making every worker aware and alert to what is happening around them. It is important to correct any problems immediately if they are discovered. If someone spots a problem while at work, they should immediately report it to their manager.
Kaizen follows a set of principles. The end product is always our starting point and we work toward the beginning. For example, if we want to improve our factory, we first fix the machines that produce the final product. Then, we fix the machines that produce components and then the ones that produce raw materials. We then fix the workers that work with those machines.
This is why it's called "kaizen" because it works step-by-step to improve everything. Once the factory is fixed, we return to the original site and work our way back until we get there.
How to measure kaizen's effectiveness in your business is essential to implement it. There are many ways you can determine if kaizen has been implemented well. One way is to examine the amount of defects on the final products. Another way is determining how much productivity increased after implementing kaizen.
A good way to determine whether kaizen has been implemented is to ask why. It was because of the law, or simply because you wanted to save some money. Did you really believe that it would be a success factor?
Let's say you answered yes or all of these questions. Congratulations! Now you're ready for kaizen.