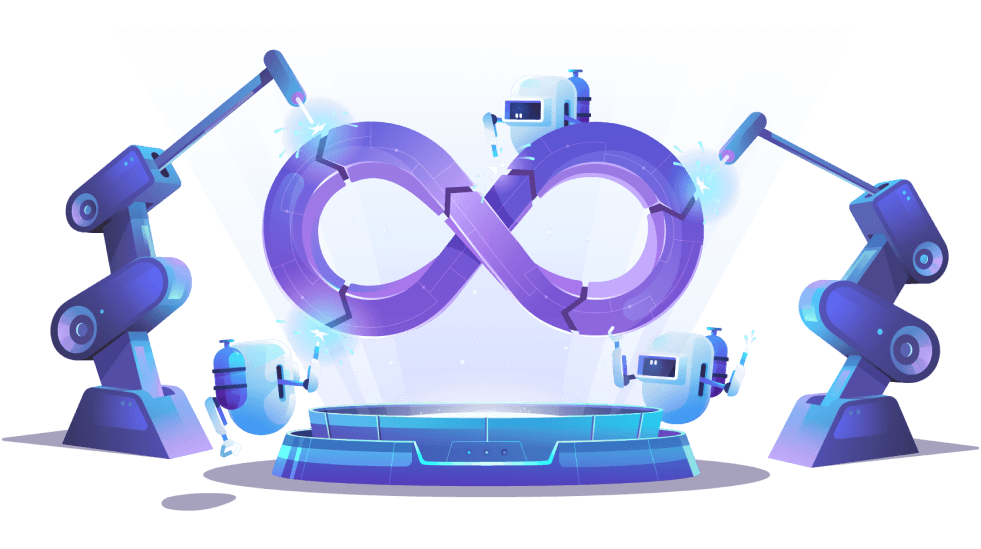
Project governance is all about identifying and tracking problems. It enables you to keep a record of what's going on, as well as keep everyone up-to-date on how the project is progressing. You can keep track of issues using a log, a spreadsheet or another tool.
There are many things that can lead to issues, from technical failures to staffing shortages. These issues can be high- or low-priority and affect the success or failure of a project. If these issues aren't addressed, they can pose a serious problem. These issues can be dealt with by using issue management methods.
To manage problems, you need a strategy and a plan. You might choose to follow multiple paths of action simultaneously. To keep everyone informed about the status of issues, you might create an issue tracking dashboard. You should be careful not misunderstand issues as risks. It is crucial to know the difference.
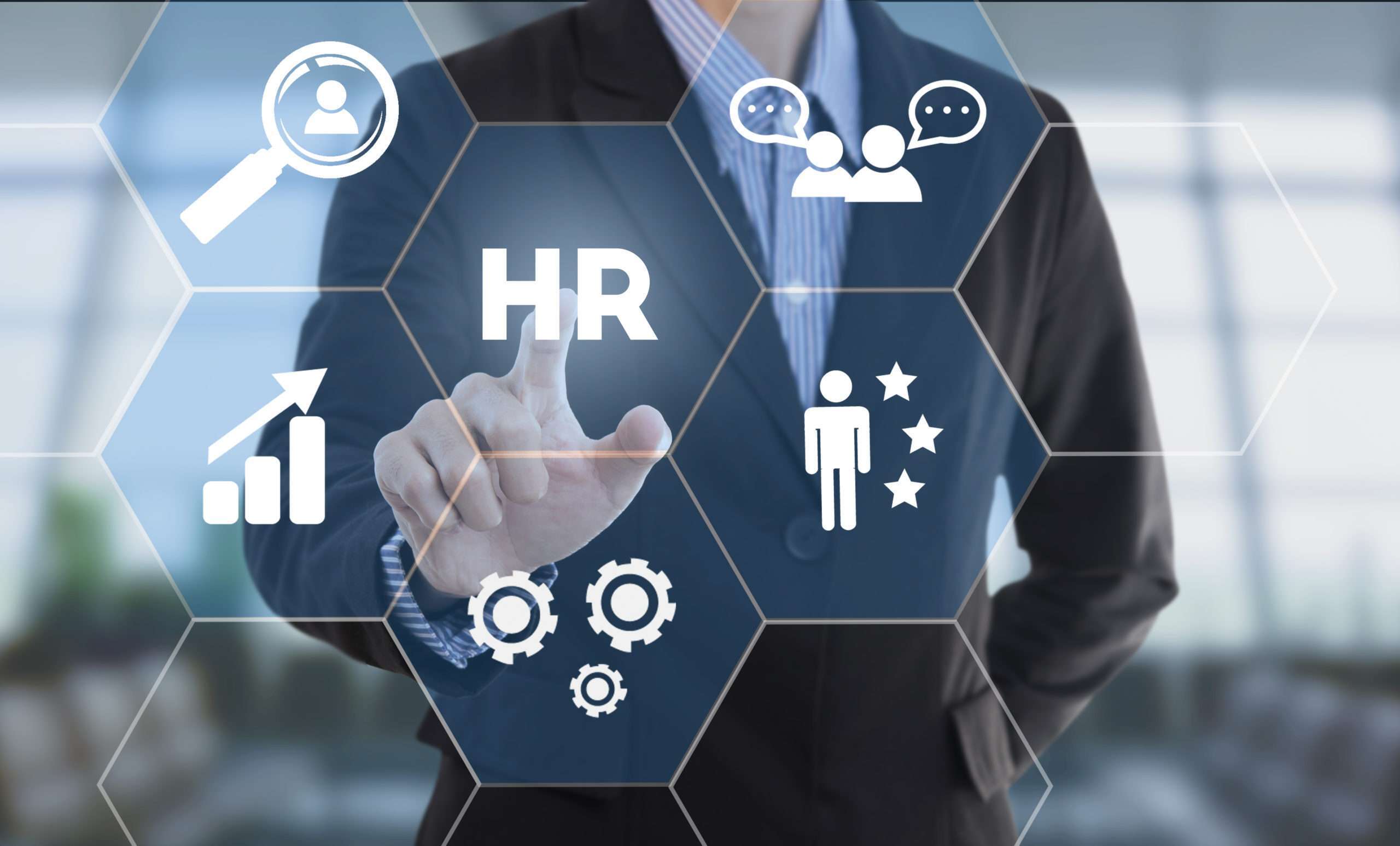
You can find issues at any level within an organization. One example is if a team member isn't skilled enough, you might have to search for another person. Issues may also be obstacles to starting a new phase or achieving a project's objectives. A project can get stalled if an issue isn't addressed. However, effective issue management will help to identify and address the problem while minimizing disruptions.
It is possible to identify issues at all levels. But you must ensure that the information is made available to those who need it. This includes people who have to report on the issue, as well as other people who may need to know how it affects the project. A simple spreadsheet might be enough to track issues in projects that aren’t as complex.
To prevent them, the first step is to identify them. It is often possible to spot small details that indicate problems. For instance, you might see that a staff person has been admitted for two weeks. If an issue is identified, you should follow it up in your issue log. You can also use it as an archival tool for later use.
There are opportunities for growth as well as problems. You may be able to hire a replacement team member if one of your team members is experiencing a medical emergency. You may be able to solve a more difficult problem by addressing the issue. It can help you spot potential issues before they become major problems.
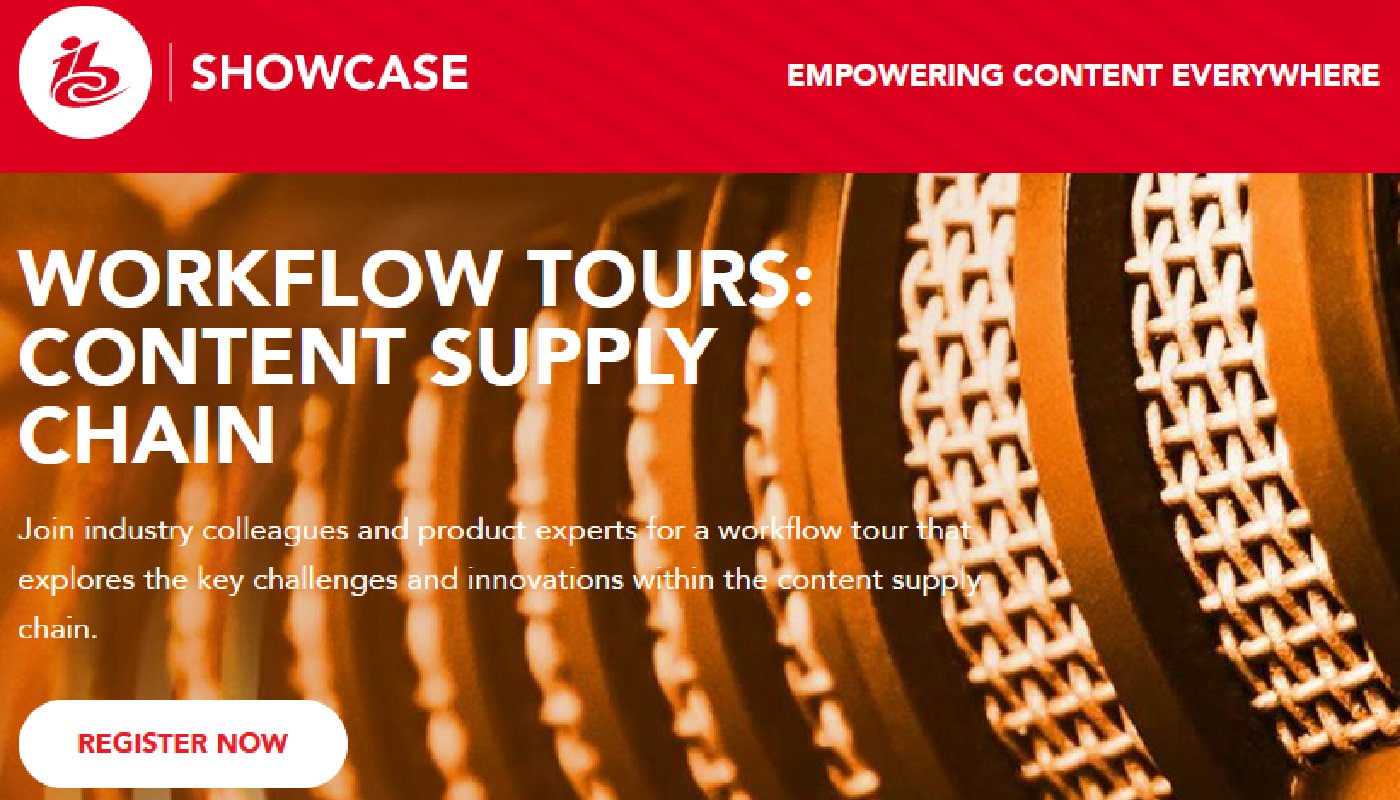
Issue management is also known as information technology service or project management. The key to project success is issue management, no matter the name. This involves tracking and identifying issues, assessing their impact, and creating a plan to address them. It is also important to ensure that the process is linked to project governance.
You have the option of keeping track of issues using a spreadsheet, an issue log or another project management tool. You should maintain an issue log with status reports and resolution comments. Also, include action items. Assign members of your team to the issues if you are able. Also, the log should include a detailed plan of resolution.
FAQ
How can we make our company culture successful?
A positive company culture creates a sense of belonging and respect in its people.
It's founded on three principal principles:
-
Everybody has something to offer.
-
People are treated fairly
-
There is mutual respect between individuals and groups
These values are reflected in the way people behave. They will treat others with kindness and consideration.
They will respect the opinions of others.
These people will inspire others to share thoughts and feelings.
A company culture encourages collaboration and communication.
People feel comfortable expressing their opinions freely without fear of reprisal.
They know mistakes will be accepted as long as they are dealt with honestly.
Finally, the company culture promotes honesty and integrity.
Everyone knows that they must always tell truth.
Everyone understands there are rules that they must follow.
Everyone does not expect to receive special treatment.
What role does a manager play in a company?
Each industry has a different role for a manager.
In general, a manager controls the day-to-day operations of a company.
He/she ensures the company meets its financial commitments and produces goods/services that customers demand.
He/she ensures employees adhere to all regulations and quality standards.
He/she is responsible for the development of new products and services, as well as overseeing marketing campaigns.
How does Six Sigma work?
Six Sigma employs statistical analysis to identify problems, measure them and analyze root causes. Six Sigma also uses experience to correct problems.
The first step in solving a problem is to identify it.
Next, data are collected and analyzed in order to identify patterns and trends.
Next, corrective steps are taken to fix the problem.
Finally, data will be reanalyzed to determine if there is an issue.
This cycle continues until the problem is solved.
Six Sigma is so beloved.
Six Sigma can be implemented quickly and produce impressive results. Six Sigma also gives companies a framework for measuring improvement and helps them focus on what is most important.
Why is it so hard to make smart business decisions?
Complex systems with many moving parts are the hallmark of businesses. The people who run them must juggle multiple priorities at once while also dealing with uncertainty and complexity.
The key to making good decisions is to understand how these factors affect the system as a whole.
To do this, you must think carefully about what each part of the system does and why. It is important to then consider how the individual pieces relate to each other.
You should also ask yourself if there are any hidden assumptions behind how you've been doing things. You might consider revisiting them if they are not.
Asking for assistance from someone else is a good idea if you are still having trouble. They might have different perspectives than you, and could offer insight that could help you solve your problem.
What is Six Sigma?
This is a method of quality improvement that emphasizes customer service, continuous learning, and customer service. The objective is to eliminate all defects through statistical methods.
Motorola developed Six Sigma in 1986 to help improve its manufacturing processes.
The idea spread quickly in the industry. Today many organizations use six-sigma techniques to improve product design.
What are management principles?
Management Concepts are the principles and practices managers use to manage people and resources. They cover topics like job descriptions (job descriptions), performance evaluations, training programmes, employee motivation and compensation systems.
Statistics
- 100% of the courses are offered online, and no campus visits are required — a big time-saver for you. (online.uc.edu)
- Your choice in Step 5 may very likely be the same or similar to the alternative you placed at the top of your list at the end of Step 4. (umassd.edu)
- This field is expected to grow about 7% by 2028, a bit faster than the national average for job growth. (wgu.edu)
- The profession is expected to grow 7% by 2028, a bit faster than the national average. (wgu.edu)
- UpCounsel accepts only the top 5 percent of lawyers on its site. (upcounsel.com)
External Links
How To
How do you do the Kaizen method?
Kaizen means continuous improvement. This term was first used by Toyota Motor Corporation in the 1950s. It refers to the Japanese philosophy that emphasizes continuous improvement through small incremental changes. It's a team effort to continuously improve processes.
Kaizen, a Lean Manufacturing method, is one of its most powerful. Kaizen is a concept where employees in charge of the production line are required to spot problems during the manufacturing process before they become major issues. This way, the quality of products increases, and the cost decreases.
The main idea behind kaizen is to make every worker aware of what happens around him/her. So that there is no problem, you should immediately correct it if something goes wrong. So, if someone notices a problem while working, he/she should report it to his/her manager.
Kaizen is based on a few principles. We always start from the end product and move toward the beginning. In order to improve our factory's production, we must first fix the machines producing the final product. First, we fix machines that produce components. Next, we fix machines that produce raw material. We then fix the workers that work with those machines.
This is why it's called "kaizen" because it works step-by-step to improve everything. After we're done with the factory, it's time to go back and fix the problem.
It is important to understand how to measure the effectiveness and implementation of kaizen in your company. There are many ways you can determine if kaizen has been implemented well. Another way to determine if kaizen is working well is to look at the quality of the products. Another way to find out how productive your company has been since you implemented kaizen is to measure the increase in productivity.
A good way to determine whether kaizen has been implemented is to ask why. Is it because the law required it or because you want to save money. Did you really think that it would help you achieve success?
Let's say you answered yes or all of these questions. Congratulations! You're now ready to get started with kaizen.