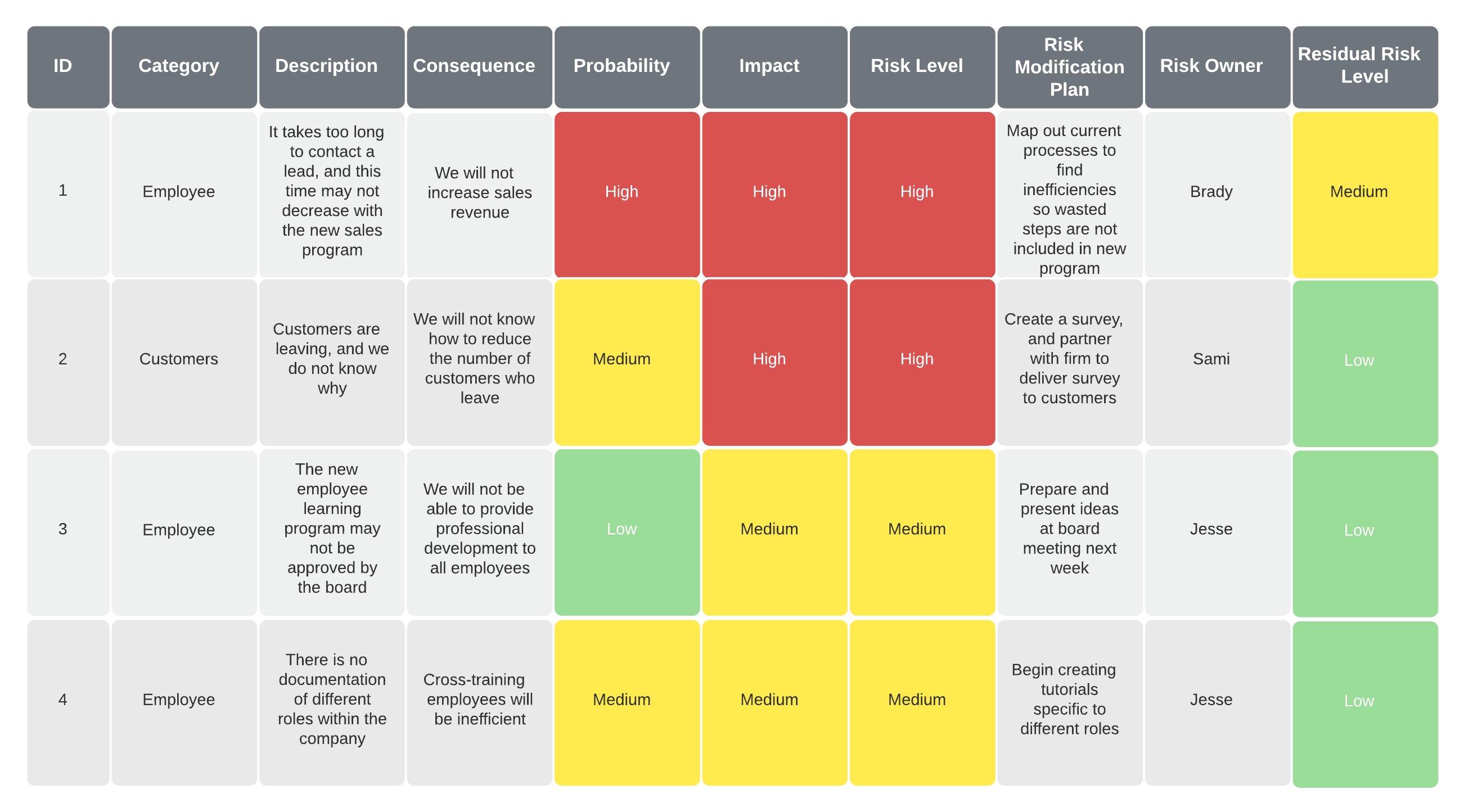
A company must satisfy 14 elements in order for it to be considered PSM. These elements include process hazard analyses and permissible exposure limits. These requirements are vital for the effective operation of a PSM program. By ensuring that the company follows these elements, a PSM program will be deemed compliant. These elements and their application to your company are covered in the sections below.
Analyses of process hazards
An essential element of any safety management program is the process hazard analysis. It helps to identify potential hazards and assess the consequences of failure. This analysis must be done with a group of people who are familiar with the process. It will also include information about human factors and past incidents. Once completed, the analysis needs to be updated every five-years. As part of a safety management program, the process of hazard analysis must also be implemented.
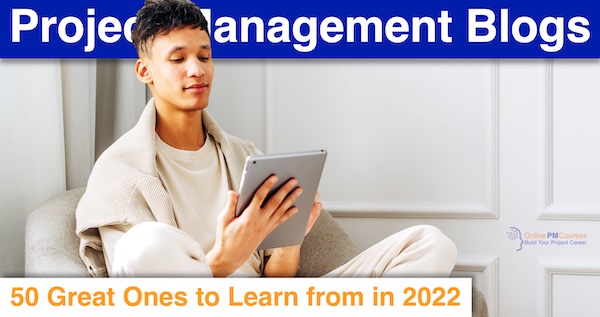
Permissible exposure limits
OSHA's Process Safety Management standard covers processes that use chemicals, gases or liquids that have been classified as hazardous. The standard applies only to businesses that manufacture or process hazardous chemicals. It does not cover hydrocarbon fuels used exclusively for workplace use, retail or well drilling. Similarly, it does not apply to remote or normally unoccupied facilities.
Physical data
PSM involves the assessment and management of hazardous products and materials. This involves knowing how to safely transport, store, and handle hazardous substances. This will result in less product waste and fewer workplace injuries. It also makes decision-making conversations easier and helps organizations prioritize health and safety. PSM is a vital part of a safe workplace. It can help companies prevent costly medical emergencies and save money.
Data on corrosivity
The PSM standard sets out requirements for how chemicals and other substances should be stored and handled. The PSM also includes requirements for emergency action plans and permit systems, and requires periodic compliance audits. No matter if your company uses hazardous substances in its production process, a PSM-compliant workplace can provide a safe environment that prevents accidents and damages.
Thermal stability data
OSHA established a standard to collect and report PSM thermal stability data. Researchers will be more aware of possible hazards and less likely to accidentally release. It will be updated regularly to reflect new research tasks. It will be available to all employees. The PSM includes information on toxicity (reactivity), corrosivity and physical properties.
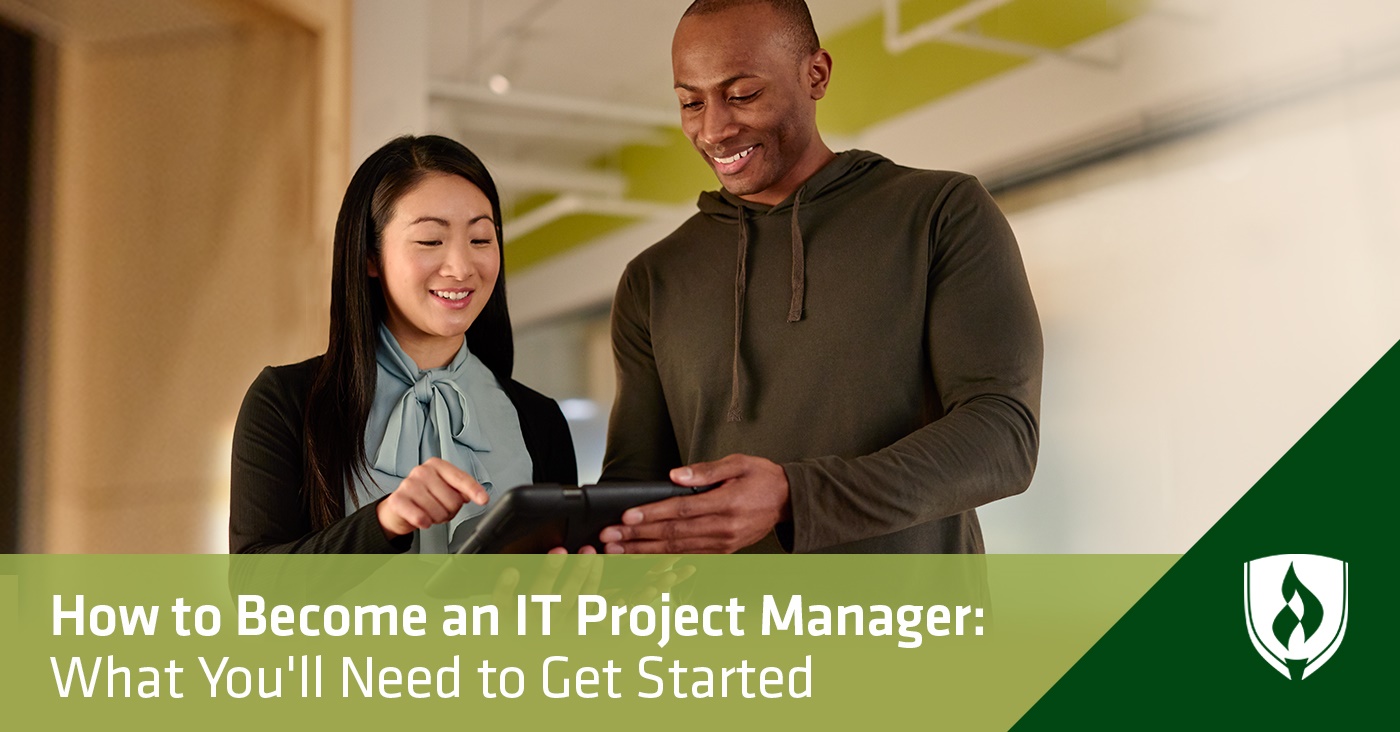
Participation clause
Process Safety Management, also known as Process Safety Management, is a methodical analytical approach to preventing accidents that are caused by hazardous chemicals (HHC). It is an important step to improving safety in process operations and should be implemented at all levels of the company, including production and maintenance departments. It has 14 elements that must be implemented, including clauses for employee participation. Here are some examples of elements and requirements.
FAQ
What are some common mistakes managers make when managing people?
Managers can make their jobs more difficult than necessary.
They may not delegate enough responsibilities to staff and fail to give them adequate support.
In addition, many managers lack the communication skills required to motivate and lead their teams.
Managers can set unrealistic expectations for their employees.
Managers may choose to solve every problem all by themselves, instead of delegating to others.
What role does a manager have in a company's success?
Different industries have different roles for managers.
A manager generally manages the day to-day operations in a company.
He/she is responsible for ensuring that the company meets all its financial obligations and produces the goods or services customers want.
He/she ensures employees adhere to all regulations and quality standards.
He/she designs new products or services and manages marketing campaigns.
What is the difference between management and leadership?
Leadership is all about influencing others. Management is about controlling others.
A leader inspires followers while a manager directs workers.
Leaders motivate people to succeed; managers keep workers on track.
A leader develops people; a manager manages people.
What is Six Sigma?
It's an approach to quality improvement that emphasizes customer service and continuous learning. It is a method that eliminates defects using statistical techniques.
Motorola created Six Sigma as part of their efforts to improve manufacturing processes in 1986.
It was quickly adopted by the industry and many companies are now using six-sigma to improve product design, production, delivery, customer service, and product design.
Statistics
- 100% of the courses are offered online, and no campus visits are required — a big time-saver for you. (online.uc.edu)
- Your choice in Step 5 may very likely be the same or similar to the alternative you placed at the top of your list at the end of Step 4. (umassd.edu)
- The profession is expected to grow 7% by 2028, a bit faster than the national average. (wgu.edu)
- As of 2020, personal bankers or tellers make an average of $32,620 per year, according to the BLS. (wgu.edu)
- This field is expected to grow about 7% by 2028, a bit faster than the national average for job growth. (wgu.edu)
External Links
How To
How can you implement a Quality Management Plan?
Quality Management Plan (QMP), which was introduced in ISO 9001:2008, provides a systematic approach to improving processes, products, and services through continual improvement. It emphasizes on how to continuously measure, analyze, control, and improve processes, product/service, and customer satisfaction.
QMP is a standard way to improve business performance. QMP's goal is to improve service delivery and production. QMPs should cover all three dimensions - Products, Processes, and Services. If the QMP focuses on one aspect, it is called "Process." QMP. When the QMP focuses on a Product/Service, it is known as a "Product" QMP. The QMP that focuses on customer relationships is known as the "Customer" QMP.
Scope is the most important element in implementing a QMP. Strategy is the second. These elements are as follows:
Scope is what the QMP covers and how long it will last. For example, if your organization wants to implement a QMP for six months, this scope will define the activities performed during the first six months.
Strategy: These are the steps taken in order to reach the goals listed in the scope.
A typical QMP has five phases: Planning (Design, Development), Implementation (Implementation), and Maintenance. Here are the details for each phase.
Planning: In this stage the QMP's objectives and priorities are established. All stakeholders involved in the project are consulted to understand their requirements and expectations. Once the objectives and priorities have been identified, it is time to plan the strategy to achieve them.
Design: This stage involves the creation of the vision, mission, strategies and tactics necessary to implement the QMP successfully. These strategies are then put into practice by creating detailed plans.
Development: Here the development team works toward building the necessary resources and capabilities to support the successful implementation.
Implementation is the actual implementation of QMP according to the plans.
Maintenance: This is an ongoing procedure to keep the QMP in good condition over time.
Several additional items should be added to the QMP.
Stakeholder Engagement: It is crucial for the QMP to be a success. They should be involved in planning, design, development and implementation of the QMP.
Project Initiation: It is essential to have a clear understanding about the problem and the solution before you can initiate a project. Also, the initiator should understand why they are doing it and what they expect.
Time Frame: It is important to consider the QMP's time frame. If you plan to implement the QMP for a short period, you can start with a simple version. If you're looking to implement the QMP over a longer period of time, you may need more detailed versions.
Cost Estimation. Cost estimation is another crucial component of QMP. You cannot plan without knowing how much money you will spend. It is therefore important to calculate the cost before you start the QMP.
QMPs are not only a document, but also a living document. This is the most important aspect of QMPs. It is constantly changing as the company changes. So, it should be reviewed periodically to make sure that it still meets the needs of the organization.