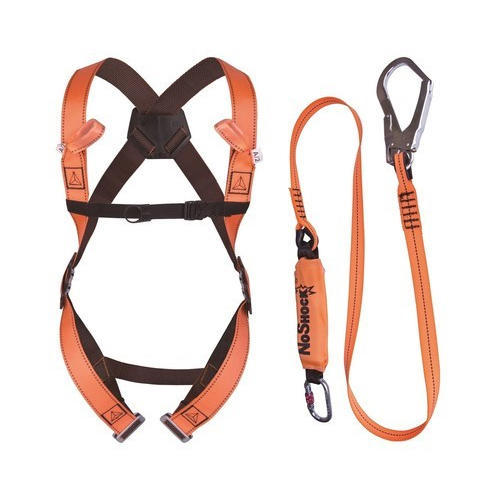
The growing popularity of green bag dumpsters is a sign of the times in junk removal. They are easier to use than traditional dumpsters and much more affordable. Learn more about this green option. We want to hear your feedback! Since we love our environment, don't you? We have all seen trash that we don’t want to dump, so it is our duty to help the environment. What are the benefits of Green bag dumpsters?
The new trend in junk removal is the green bag dumpster
The latest trend in junk removal is the green bag dumpster. These are a more convenient option to traditional dumpsters and can be easily transported from one location to the next. These dumpsters are typically filled with trash and debris that can then be disposed of later by a junk elimination company. Green bag dumpsters are convenient but have their drawbacks. These containers can only hold limited amounts of trash. Also, they are not always available in all locations.
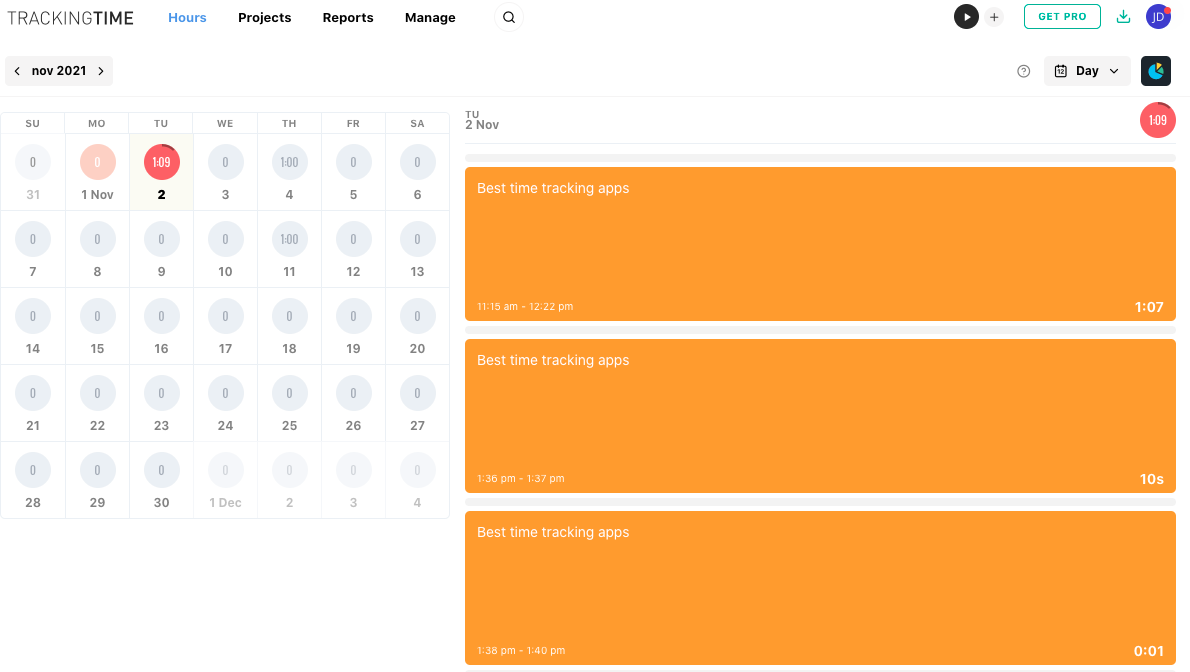
They are cheaper
If you're planning on renting a dumpster in your area, you might be wondering if Bag dumpsters are cheaper. Bagsters can be moved without a crane, but they require more structure than a regular roll-off dumpster. Dumpster bags may not always be available in your area. Before making a purchase, make sure you research the availability. You can also book roll-off dumpster pickup online or over the phone. Make sure to reserve your dumpster well in advance.
They are much easier to place.
Bag dumpsters are for non-electronic and non-hazardous materials. These dumpsters can be placed and moved more easily than traditional roll off dumpsters. This type of dumpster is not recommended for large, heavy items. They are more susceptible of being damaged by sharp objects. A bag dumpster may appear sturdy, but its collapsibility makes it more easily knocked over.
They're eco-friendly
A great choice for construction and remodeling projects is the Big Blue Bag. This versatile bag can handle untreated wood, concrete, asphalt and concrete. It is also easy to carry and place. The bag also has handles that make it easy to carry. And because it is made from 100% recycled material, it is highly eco-friendly. Bag dumpsters can also be used for other purposes. It can be reused for other jobs once it has been filled. You can fold it so it can be easily stored away.
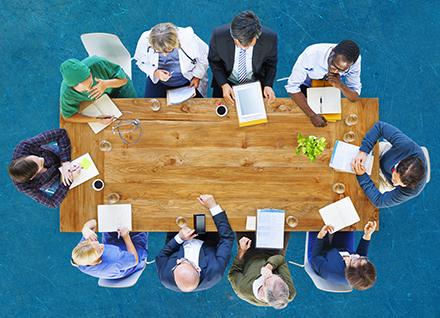
They come with restrictions
Bag dumpsters make a great choice for getting rid of unwanted items in your home. There are certain rules that must be observed when using these dumpsters. Bags cannot be filled more than half full. These bags are not allowed to be placed outside for more then 30 days. If you have too much junk to carry around, another bag might be a better option. This additional service will cost you extra money. Also, you should check to see if you can place certain appliances or electronics in a bag dumpster.
FAQ
What does "project management" mean?
Management is the act of managing activities in order to complete a project.
We include defining the scope of the project, identifying the requirements, preparing the budget, organizing the project team, scheduling the work, monitoring progress, evaluating results, and closing down the project.
Six Sigma is so popular.
Six Sigma can be implemented quickly and produce impressive results. Six Sigma provides a framework to measure improvements and allows companies to focus on the most important things.
What are the 4 major functions of management
Management is responsible to plan, organize, direct, and control people and resources. This includes setting goals, developing policies and procedures, and creating procedures.
Management helps an organization achieve its objectives by providing direction, coordination, control, leadership, motivation, supervision, training, and evaluation.
These are the four major functions of management:
Planning – Planning involves deciding what needs to happen.
Organizing: Organizing refers to deciding how things should work.
Direction - This is the art of getting people to follow your instructions.
Controlling – Controlling is the process of ensuring that tasks are completed according to plan.
What's the difference between Six Sigma and TQM?
The main difference between these two quality management tools is that six sigma focuses on eliminating defects while total quality management (TQM) focuses on improving processes and reducing costs.
Six Sigma can be described as a strategy for continuous improvement. It emphasizes the elimination of defects by using statistical methods such as control charts, p-charts, and Pareto analysis.
This method has the goal to reduce variation of product output. This is accomplished through identifying and correcting root causes.
Total quality management is the measurement and monitoring of all aspects within an organization. This includes training employees to improve their performance.
It is often used to increase productivity.
What are the three basic management styles?
These are the three most common management styles: participative (authoritarian), laissez-faire (leavez-faire), and authoritarian. Each style is unique and has its strengths as well as weaknesses. Which style do yo prefer? Why?
Autoritarian – The leader sets the direction for everyone and expects them to follow. This style is most effective when an organization is large, stable, and well-run.
Laissez-faire – The leader gives each individual the freedom to make decisions for themselves. This style works best when the organization is small and dynamic.
Participative – Leaders are open to suggestions and ideas from everyone. This is a great style for smaller organizations that value everyone.
How does a manager motivate his/her employees?
Motivation is the desire to do well.
Enjoyable activities can motivate you.
You can also get motivated by seeing your contribution to the success or the improvement of the organization.
For example, if you want to become a doctor, you'll probably find it more motivating to see patients than to study medicine books all day.
Another type of motivation comes from within.
One example is a strong sense that you are responsible for helping others.
You might even enjoy the work.
Ask yourself why you aren't feeling motivated.
Then, consider ways you could improve your motivation.
What is a basic management tool that can be used for decision-making?
A decision matrix can be a simple, but effective tool to assist managers in making decisions. It helps them think systematically about all the options available to them.
A decision matrix represents alternatives in rows and columns. This makes it easy for you to see how each option affects other options.
In this example, we have four possible alternatives represented by the boxes on the left side of the matrix. Each box represents an option. The status quo (the current condition) is shown in the top row, and what would happen if there was no change?
The effect of Option 1 can be seen in the middle column. In this example, it would lead to an increase in sales of between $2 million and $3 million.
The next two columns show the effects of choosing Options 2 and 3. These positive changes result in increased sales of $1 million and $500,000. But, they also have some negative consequences. Option 2, for example, increases the cost by $100 000 while Option 3 decreases profits by $200 000.
The final column shows results of choosing Option 4. This results in a decrease of sales by $1,000,000
A decision matrix has the advantage that you don’t have to remember where numbers belong. The best thing about a decision matrix is that you can simply look at the cells, and immediately know whether one option is better or not.
This is because your matrix has already done the hard work. It's as easy as comparing numbers in the appropriate cells.
Here's an example of how you might use a decision matrix in your business.
You want to decide whether or not to invest more money into advertising. You'll be able increase your monthly revenue by $5000 if you do. However, additional expenses of $10 000 per month will be incurred.
You can calculate the net result of investing in advertising by looking at the cell directly below the one that says "Advertising." That number is $15 thousand. Therefore, you should choose to invest in advertising since it is worth more than the cost involved.
Statistics
- This field is expected to grow about 7% by 2028, a bit faster than the national average for job growth. (wgu.edu)
- Hire the top business lawyers and save up to 60% on legal fees (upcounsel.com)
- 100% of the courses are offered online, and no campus visits are required — a big time-saver for you. (online.uc.edu)
- The average salary for financial advisors in 2021 is around $60,000 per year, with the top 10% of the profession making more than $111,000 per year. (wgu.edu)
- The profession is expected to grow 7% by 2028, a bit faster than the national average. (wgu.edu)
External Links
How To
How can Lean Manufacturing be done?
Lean Manufacturing is a method to reduce waste and increase efficiency using structured methods. They were developed in Japan by Toyota Motor Corporation (in the 1980s). The goal was to produce quality products at lower cost. Lean manufacturing seeks to eliminate unnecessary steps and activities in the production process. It consists of five basic elements: pull systems, continuous improvement, just-in-time, kaizen (continuous change), and 5S. It is a system that produces only the product the customer requests without additional work. Continuous improvement is the continuous improvement of existing processes. Just-in-time refers to when components and materials are delivered directly to the point where they are needed. Kaizen stands for continuous improvement. Kaizen can be described as a process of making small improvements continuously. Last but not least, 5S is for sort. These five elements can be combined to achieve the best possible results.
Lean Production System
Six key concepts underlie the lean production system.
-
Flow - focuses on moving information and materials as close to customers as possible.
-
Value stream mapping is the ability to divide a process into smaller tasks, and then create a flowchart that shows the entire process.
-
Five S’s - Sorted, In Order. Shine. Standardize. And Sustain.
-
Kanban: Use visual signals such stickers, colored tape, or any other visual cues, to keep track your inventory.
-
Theory of constraints - identify bottlenecks in the process and eliminate them using lean tools like kanban boards;
-
Just-in Time - Send components and material directly to the point-of-use;
-
Continuous improvement: Make incremental improvements to the process instead of overhauling it completely.