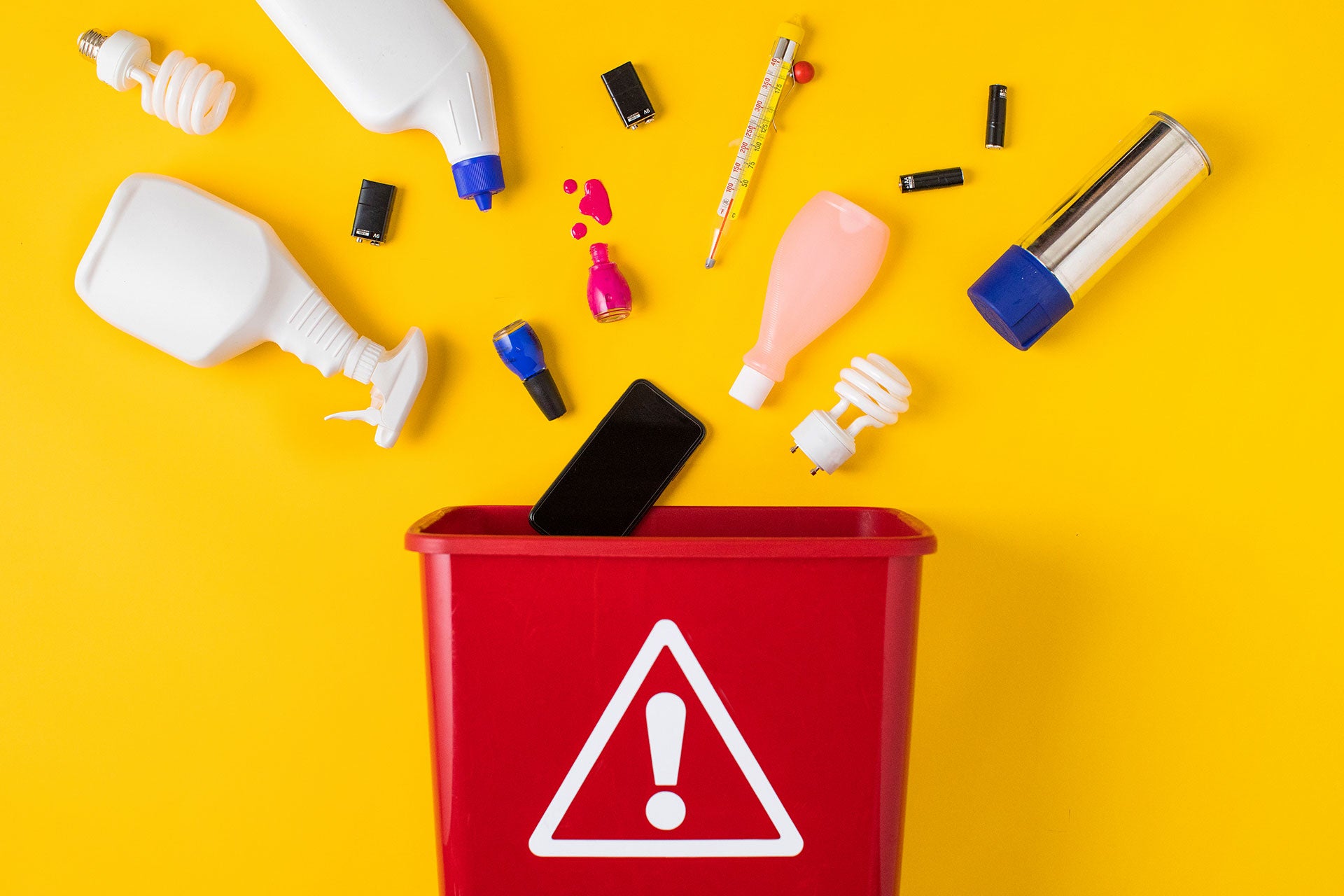
Articles on supply chain management are published regularly in a variety of journals. The number and type of articles published will depend on the journal. Most articles are focused upon SMEs or high-demand items. Some articles will discuss agency theory and how it affects supply chain management. This section gives an overview of articles published in different journals.
Trends in supply chain management articles
Businesses are dependent on supply chains for their survival. They need to function seamlessly, no matter whether it's online or offline, in order to satisfy customer expectations. The disruption of a supply chain can lead to disruptions in the business' entire operations, including a COVID-19-related pandemic and a labor shortfall. However, supply chain trends and statistics can help prepare businesses for any changes that may arise.
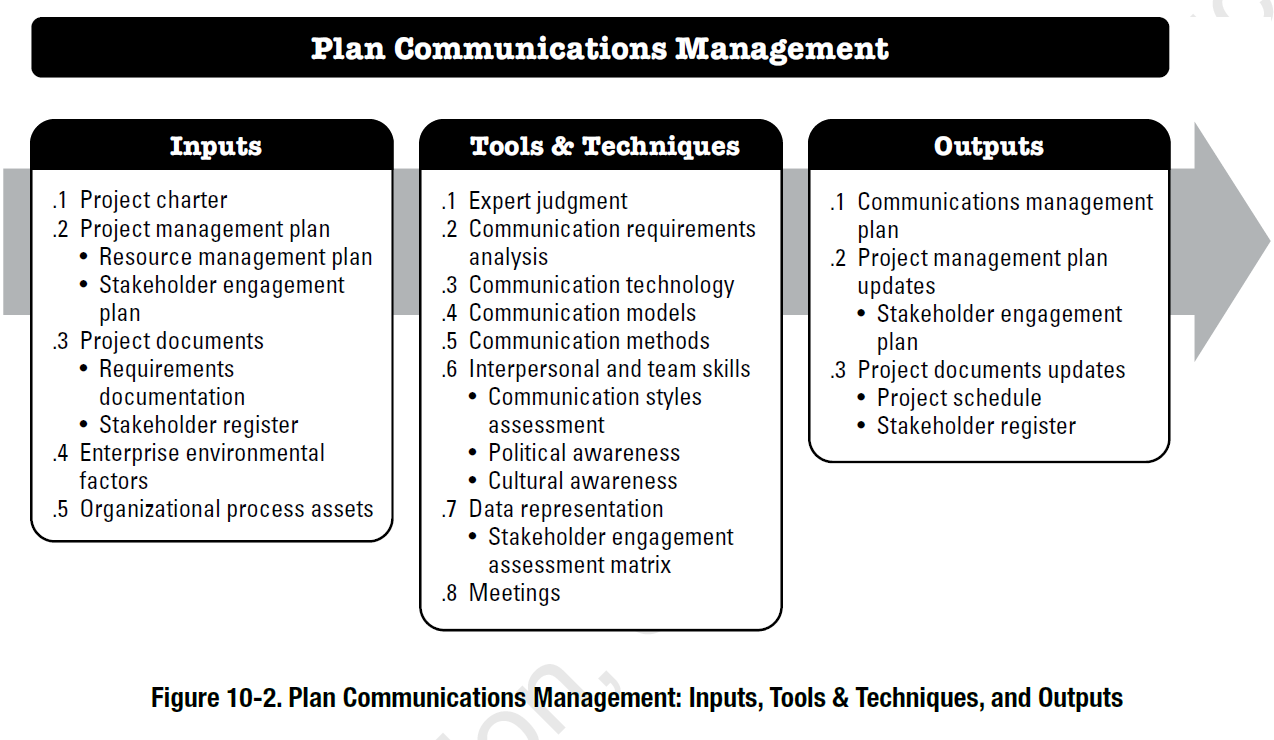
Supply chains are evolving as a result of several factors, including customer expectations and technological advances. Companies must be capable of managing multiple customer channels and fulfilment models as well as payment options and physical systems. Companies are increasingly turning to artificial intelligence (AI), to optimize their supply chains. This technology can not only help save money, it can also speed things up.
Association of related researchers for articles on supply chain management
The Association of Affiliated Researchers in Articles on Supply Chain Management produces a ranking of supply chains management research output. Its basis is the number of publications in previous five years. Submissions are assessed for their relevance to the program theme, the rigor and the meaningful advancement of supply chain management knowledge.
AAF publishes research reports on a wide variety of topics, including the role and importance of supply chain professionals within the global economy. These research findings provide insight into trends in the supply chain and the procurement industry. Topics include forecasting, big data and inventory management. Sales and operations planning are also covered.
The majority of articles concern SMEs.
Although the majority of articles on supply-chain management focus on large, global organizations, others focus on small and medium enterprises (SMEs). Zowada (2011) states that the key to linking is the ability for SMEs to be adaptable and flexible, which are essential factors in creating a competitive advantage.
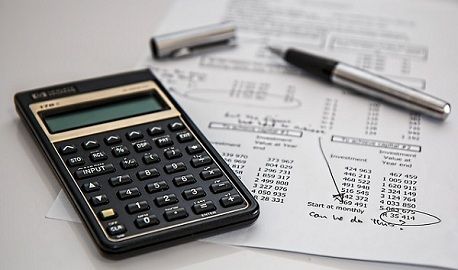
SMEs are an essential part of most economies and societies, making outsized contributions to GDP, exports, employment, and livelihoods. However, they are increasingly facing threats that could stifle their growth. Luckily, governments have the opportunity to learn from past successes and to create programs that help SMEs succeed in today's world.
FAQ
How can we create a successful company culture?
Successful company culture is one where people feel valued and respected.
It's based on three main principles:
-
Everybody can contribute something valuable
-
People are treated fairly
-
Individuals and groups can have mutual respect
These values can be seen in the behavior of people. They will treat others with respect and kindness.
They will be respectful of the opinions of other people.
They will also encourage others to share their ideas and feelings.
Additionally, the company culture encourages open communication as well as collaboration.
People feel free to express their views openly without fear of reprisal.
They are aware that mistakes can be accepted if they are treated honestly.
Finally, the company culture promotes honesty and integrity.
Everyone knows that they must always tell the truth.
Everyone knows that there are rules and regulations that apply to them.
And no one expects special treatment or favors.
Why is it so hard to make smart business decisions?
Complex business systems have many moving parts. People who manage them have to balance multiple priorities while dealing with complexity and uncertainty.
It is important to understand the effects of these factors on the system in order to make informed decisions.
This requires you to think about the purpose and function of each component. It's important to also consider how they interact with each other.
It is also worth asking yourself if you have any unspoken assumptions about how you have been doing things. If you don't have any, it may be time to revisit them.
Try asking for help from another person if you're still stuck. You may be able to see things from a different perspective than you are and gain insight that can help you find a solution.
What kind people use Six Sigma?
People who have worked with statistics and operations research will usually be familiar with the concepts behind six sigma. But anyone can benefit from it.
This requires a lot of dedication, so only people with great leadership skills can make the effort to implement it.
What is TQM, exactly?
The industrial revolution was when companies realized that they couldn't compete on price alone. This is what sparked the quality movement. To remain competitive, they had to improve quality as well as efficiency.
Management developed Total Quality Management to address the need for improvement. It focused on all aspects of an organisation's performance. It included continuous improvement processes, employee involvement, and customer satisfaction.
What are the steps of the management decision-making process?
Managers face complex and multifaceted decision-making challenges. It involves many elements, including analysis, strategy. planning. implementation. measurement. evaluation. feedback.
The key thing to remember when managing people is that they are human beings just as you are and therefore make mistakes. You can always improve your performance, provided you are willing to make the effort.
This video explains the process of decision-making in Management. We will discuss the various types of decisions, and why they are so important. Every manager should be able to make them. The following topics will be covered:
What are the four major functions of Management?
Management is responsible in planning, organizing and directing people and resources. Management also involves setting goals and developing policies.
Organizations can achieve their goals through management. This includes leadership, coordination, control and motivation.
Management has four primary functions:
Planning - Planning involves determining what needs to be done.
Organizing - Organizing involves deciding how things should be done.
Directing – This means to get people to follow directions.
Controlling: Controlling refers to making sure that people do what they are supposed to.
What is the role of a manager in a company?
Each industry has a different role for a manager.
The manager oversees the day-to-day activities of a company.
He/she ensures that the company meets its financial obligations and produces goods or services that customers want.
He/she will ensure that employees follow all rules and regulations, and adhere to quality standards.
He/she plans new products and services and oversees marketing campaigns.
Statistics
- Hire the top business lawyers and save up to 60% on legal fees (upcounsel.com)
- Our program is 100% engineered for your success. (online.uc.edu)
- The BLS says that financial services jobs like banking are expected to grow 4% by 2030, about as fast as the national average. (wgu.edu)
- 100% of the courses are offered online, and no campus visits are required — a big time-saver for you. (online.uc.edu)
- As of 2020, personal bankers or tellers make an average of $32,620 per year, according to the BLS. (wgu.edu)
External Links
How To
What is Lean Manufacturing?
Lean Manufacturing is a method to reduce waste and increase efficiency using structured methods. They were developed by Toyota Motor Corporation in Japan during the 1980s. The aim was to produce better quality products at lower costs. Lean manufacturing eliminates unnecessary steps and activities from a production process. It consists of five basic elements: pull systems, continuous improvement, just-in-time, kaizen (continuous change), and 5S. Pull systems are able to produce exactly what the customer requires without extra work. Continuous improvement means continuously improving on existing processes. Just-in time refers to components and materials being delivered right at the place they are needed. Kaizen means continuous improvement. Kaizen involves making small changes and improving continuously. The 5S acronym stands for sort in order, shine standardize and maintain. These five elements are used together to ensure the best possible results.
Lean Production System
Six key concepts form the foundation of the lean production system:
-
Flow - focus on moving material and information as close to customers as possible;
-
Value stream mapping: This is a way to break down each stage into separate tasks and create a flowchart for the entire process.
-
Five S's – Sort, Put In Order Shine, Standardize and Sustain
-
Kanban - use visual signals such as colored tape, stickers, or other visual cues to keep track of inventory;
-
Theory of constraints - identify bottlenecks in the process and eliminate them using lean tools like kanban boards;
-
Just-in time - Get components and materials delivered right at the point of usage;
-
Continuous improvement is making incremental improvements to your process, rather than trying to overhaul it all at once.