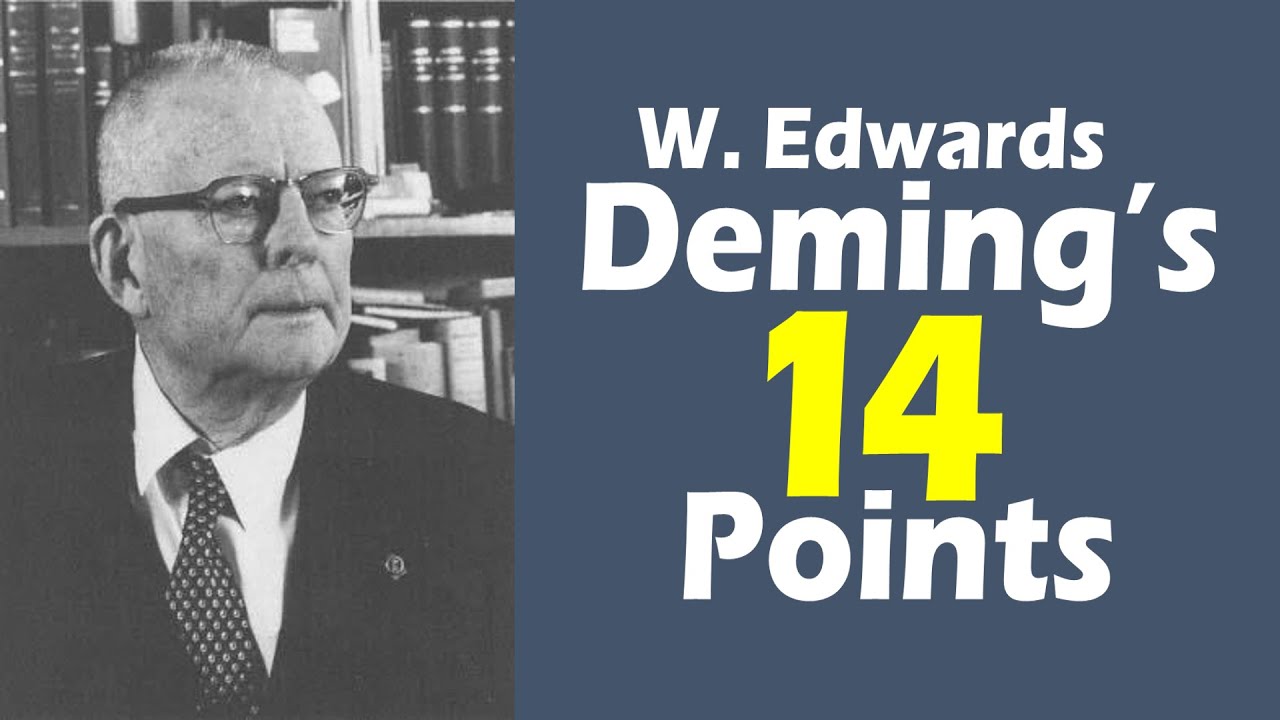
A management strategy refers to the process of creating and implementing major objectives. It requires taking responsibility for stakeholders. It is important to take into account several factors when creating a strategy. A management strategy must be specific and manageable. To achieve its goals, a strategy should be implemented in a coordinated fashion.
Techniques used to achieve individual goals
Tactics are actions that add to a strategy in management. They help break down a strategy into specific tasks with due dates to create an accurate timeline. Tactics is the specific task within a strategy. They are the second half of "how" category. Strategies explain what goals the project should achieve, while tactics outline how to execute those goals.
Management teams should closely link their operational goals to the overall organizational goals. These goals should be consistent with the organization's mission and vision. Employees will know which goals they are responsible for. Working in harmony with the whole organization will make it easier to achieve your goals.
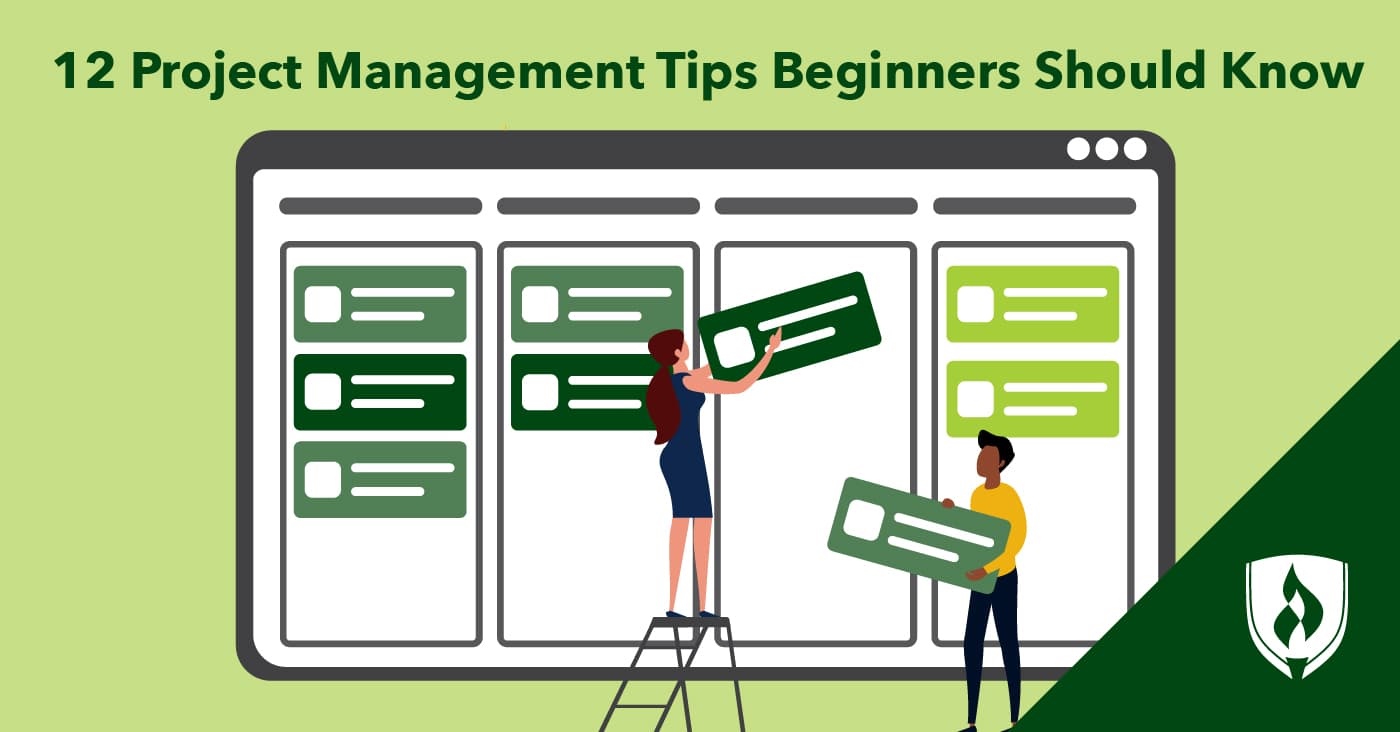
Tactics executed in a coordinated manner
Tactics are the activities carried out in a business to achieve goals and objectives. They include creating and delivering value, as well as expanding it. Tactics help a business maintain its unique position in the market by aligning its resources. These activities are designed to support and strengthen the strategy, and provide consistent customer experiences.
Tactics and strategy are terms that originated in the military and have been adopted for business purposes. Strategy is the overall plan for achieving a goal. Tactics are the steps and actions taken to achieve that goal. Strategy is the long-term vision for the organization that defines the goal.
Organizational goals can be achieved using tactics
Tactics are specific actions taken in an effort to achieve an organization’s goals. These tactics are part of a strategy. This is a blueprint that describes the company's future image. These blueprints are made to work using tactics that integrate all resources. They may be used to achieve a specific goal or to be a cautionary measure if the original strategy doesn't meet expectations.
It is essential to establish measurable metrics to evaluate the effectiveness and efficiency of any tactic. A number of events per year can be set, for example, to encourage more event-taking. They can also define the number of events held per month or week. Assigning measurable values to tactics makes it possible to see if they're working and whether they're achieving the goals of the company.
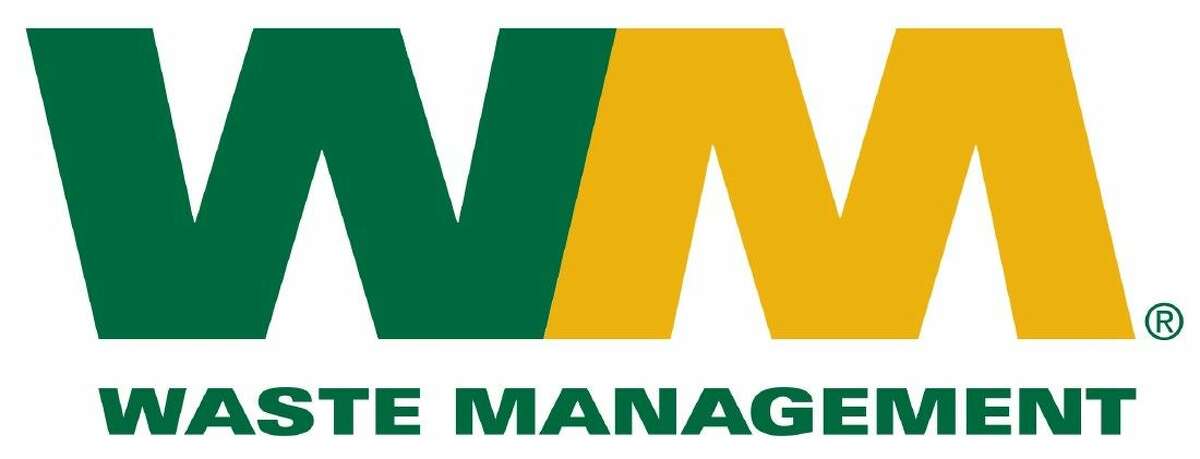
The second step is to identify the tactics you can use to achieve your goals. These tactics are actionable and can be easily implemented by a team. They are defined by managers and can be evaluated with well-defined metrics. Also, tactical plans usually include details about implementation and timelines.
FAQ
Why is it so hard to make smart business decisions?
Complex systems and many moving parts make up businesses. They require people to manage multiple priorities and deal with uncertainty and complexity.
The key to making good decisions is to understand how these factors affect the system as a whole.
This requires you to think about the purpose and function of each component. Then, you need to think about how these pieces interact with one another.
Ask yourself if there are hidden assumptions that have influenced your behavior. If so, it might be worth reexamining them.
For help, ask someone else if you're still stumped after all the above. They may see things differently from you and have insights that could help you find a solution.
What is TQM and how can it help you?
The industrial revolution was when companies realized that they couldn't compete on price alone. This is what sparked the quality movement. They needed to improve the quality and efficiency of their products if they were to be competitive.
Management developed Total Quality Management to address the need for improvement. It focused on all aspects of an organisation's performance. It included continuous improvement, employee involvement and customer satisfaction.
What are the 4 major functions of management
Management is responsible for planning, organizing, directing, and controlling people and resources. It also includes developing policies and procedures and setting goals.
Management assists an organization in achieving its goals by providing direction, coordination and control, leadership, motivation, supervision and training, as well as evaluation.
The following are the four core functions of management
Planning – Planning involves deciding what needs to happen.
Organizing – Organizing means deciding how to organize things.
Directing – This means to get people to follow directions.
Controlling - This is the ability to control people and ensure that they do their jobs according to plan.
What is the difference of leadership and management?
Leadership is about influence. Management is about controlling others.
Leaders inspire followers, while managers direct workers.
A leader motivates people and keeps them on task.
A leader develops people; a manager manages people.
What is Kaizen?
Kaizen is a Japanese term meaning "continuous improvement." It is a philosophy that encourages employees to constantly look for ways to improve their work environment.
Kaizen is based upon the belief that each person should be capable of doing his or her job well.
What are the steps to take in order to make a management decision?
The decision-making process for managers is complex and multifaceted. This involves many factors including analysis, strategy and planning, implementation, measurement and evaluation, feedback, feedback, and others.
Management of people requires that you remember that they are just as human as you are, and can make mistakes. You are always capable of improving yourself, and there's always room for improvement.
This video shows you how management makes decisions. We discuss the different types of decisions and why they are important, every manager should know how to navigate them. These topics are covered in this course:
What are the three basic management styles?
The three major management styles are authoritarian (left-faire), participative and laissez -faire. Each style is unique and has its strengths as well as weaknesses. Which style do YOU prefer? Why?
Authority - The leader is the one who sets the direction and expects everyone in the organization to follow it. This style is most effective when an organization is large, stable, and well-run.
Laissez-faire is a leader who allows everyone to make their own decisions. This style works best when the organization is small and dynamic.
Participative - Leaders listen to all ideas and suggestions. This is a great style for smaller organizations that value everyone.
Statistics
- This field is expected to grow about 7% by 2028, a bit faster than the national average for job growth. (wgu.edu)
- The profession is expected to grow 7% by 2028, a bit faster than the national average. (wgu.edu)
- Our program is 100% engineered for your success. (online.uc.edu)
- UpCounsel accepts only the top 5 percent of lawyers on its site. (upcounsel.com)
- 100% of the courses are offered online, and no campus visits are required — a big time-saver for you. (online.uc.edu)
External Links
How To
How is Lean Manufacturing done?
Lean Manufacturing uses structured methods to reduce waste, increase efficiency and reduce waste. They were developed by Toyota Motor Corporation in Japan during the 1980s. It was designed to produce high-quality products at lower prices while maintaining their quality. Lean manufacturing emphasizes removing unnecessary steps from the production process. It includes five main elements: pull systems (continuous improvement), continuous improvement (just-in-time), kaizen (5S), and continuous change (continuous changes). Pull systems allow customers to get exactly what they want without having to do extra work. Continuous improvement is constantly improving upon existing processes. Just-in–time refers when components or materials are delivered immediately to their intended destination. Kaizen means continuous improvement, which is achieved by implementing small changes continuously. Five-S stands for sort. It is also the acronym for shine, standardize (standardize), and sustain. To achieve the best results, these five elements must be used together.
Lean Production System
Six key concepts make up the lean manufacturing system.
-
Flow - The focus is on moving information and material as close as possible to customers.
-
Value stream mapping- This allows you to break down each step of a process and create a flowchart detailing the entire process.
-
Five S's - Sort, Set In Order, Shine, Standardize, and Sustain;
-
Kanban is a visual system that uses visual cues like stickers, colored tape or stickers to keep track and monitor inventory.
-
Theory of constraints - identify bottlenecks in the process and eliminate them using lean tools like kanban boards;
-
Just-in Time - Send components and material directly to the point-of-use;
-
Continuous improvement: Make incremental improvements to the process instead of overhauling it completely.