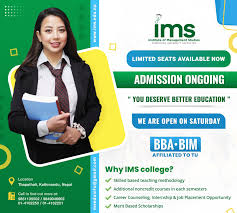
The inherent directionality of supply network networks is not captured by a business flow metric. There are many levels of dependencies in a supply network, and they often interact. A business flow metric does not capture the intrinsic directionality of information flows within a network. Understanding and considering these issues is essential for the development of a digital supply network.
Sustainability
Multinational corporations recognize the importance of sustainability in supply networks as a key element of their supply chain management strategy. Many companies have made sustainability an important priority and committed themselves to using sustainable suppliers. However, many lower-level suppliers do not follow sustainability standards, posing serious risks for businesses. This article examines three major MNCs' supply networks. The authors found some best practices that companies could adopt to counter this problem. These include setting long-term sustainability targets and including lower-tier suppliers within the sustainability strategy.

Companies must establish targets and measure their progress in order to show how they are improving their supply chain. They must also involve all stakeholders in the supply chain, including internal staff who drive change and consumers. The goal should not be to prove the benefits to business of sustainable supply networks but to create the governance and organizational structures necessary to ensure that the sustainability efforts are a success.
Vertical disintegration in supply chains
For firms, vertical disintegration of supply chain can have many negative consequences. Apart from the potential for greater costs and losses, it can also lead to changes in organisational structures and hierarchies. To increase their overall competitiveness and reduce their participation in upstream or downstream activities, some companies may consider this option. This approach is not always the best and should be used only in certain circumstances.
Vertical integration's main drawback is its limitation of flexibility. This is because vertical integration makes it conform to certain trends within a segment. It may prove difficult for retailers to adopt new technology if their competition already uses it. To keep up with its competition, the parent company would need to invest in new technology. Integration can be complicated by rapidly changing technologies. Furthermore, companies often face challenges integrating different technologies from different parts of their supply chains, which can be costly.
Performance implications of a Digital Supply Network
Digital supply chains can have many benefits. They are more efficient, resilient, and cost-savings. However, they can also increase cybersecurity risk. However, there are several approaches companies can use to mitigate these risks. Let's look at some. These methods involve data analytics. This technology gives businesses insight into customer preferences and allows them to improve their products. By incorporating shared data, companies can better predict potential problems, and make informed decisions.
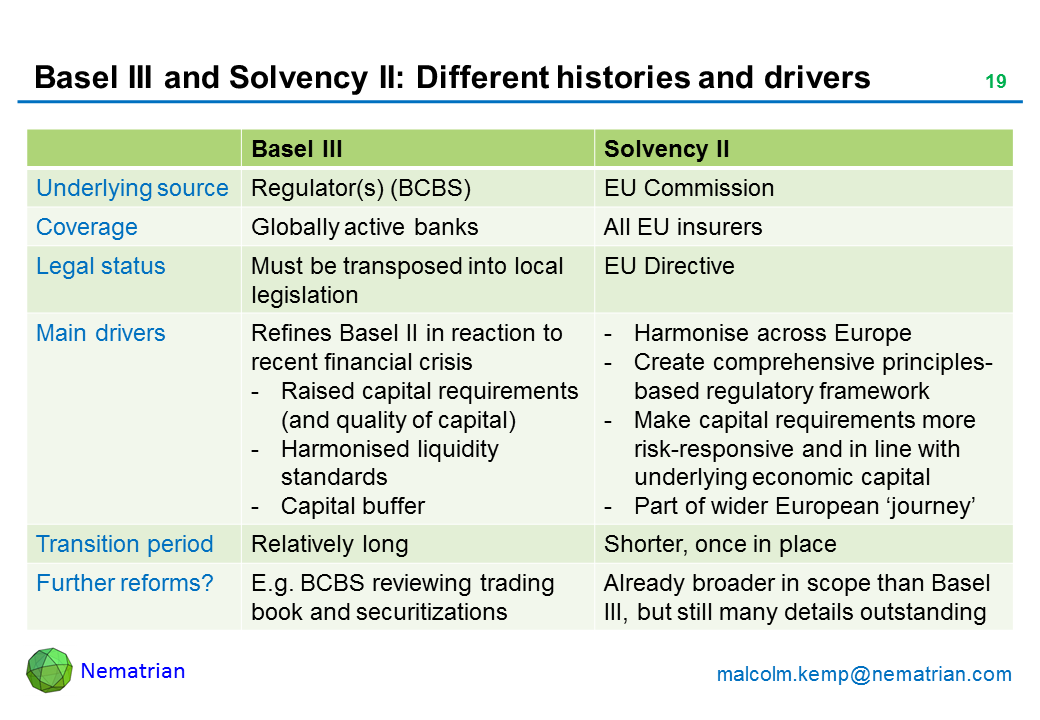
Assessing your supply chain is the first step towards digitalization. This will help you identify and mitigate any risks or issues, as well any potential complications. This will allow you to create an action plan that minimizes any potential dangers. Once you have a clear picture of your goals, it is time to work with your partner. This will ensure that all stakeholders are satisfied with the digital supply chain.
FAQ
What role does a manager have in a company's success?
Managers' roles vary from industry to industry.
A manager is generally responsible for overseeing the day to day operations of a company.
He/she ensures the company meets its financial commitments and produces goods/services that customers demand.
He/she will ensure that employees follow all rules and regulations, and adhere to quality standards.
He/she oversees marketing campaigns and plans new products.
What do we mean when we say "project management"?
That is the management of all activities associated with a project.
This includes defining the scope, identifying the requirements and preparing the budget. We also organize the project team, schedule the work, monitor progress, evaluate results, and close the project.
Why is Six Sigma so popular?
Six Sigma is easy and can deliver significant results. Six Sigma also gives companies a framework for measuring improvement and helps them focus on what is most important.
What are some common mistakes managers make?
Managers can make their jobs more difficult than necessary.
They may not delegate enough responsibilities to staff and fail to give them adequate support.
Additionally, many managers lack communication skills that are necessary to motivate and direct their teams.
Managers set unrealistic expectations and make it difficult for their team.
Some managers may try to solve every problem themselves instead of delegating responsibility to others.
Statistics
- The profession is expected to grow 7% by 2028, a bit faster than the national average. (wgu.edu)
- Hire the top business lawyers and save up to 60% on legal fees (upcounsel.com)
- Your choice in Step 5 may very likely be the same or similar to the alternative you placed at the top of your list at the end of Step 4. (umassd.edu)
- This field is expected to grow about 7% by 2028, a bit faster than the national average for job growth. (wgu.edu)
- The average salary for financial advisors in 2021 is around $60,000 per year, with the top 10% of the profession making more than $111,000 per year. (wgu.edu)
External Links
How To
How does Lean Manufacturing work?
Lean Manufacturing methods are used to reduce waste through structured processes. They were created in Japan by Toyota Motor Corporation during the 1980s. The goal was to produce quality products at lower cost. Lean manufacturing eliminates unnecessary steps and activities from a production process. It consists of five basic elements: pull systems, continuous improvement, just-in-time, kaizen (continuous change), and 5S. It is a system that produces only the product the customer requests without additional work. Continuous improvement is constantly improving upon existing processes. Just-in–time refers when components or materials are delivered immediately to their intended destination. Kaizen is continuous improvement. This can be achieved by making small, incremental changes every day. Finally, 5S stands for sort, set in order, shine, standardize, and sustain. These five elements are used together to ensure the best possible results.
Lean Production System
Six key concepts are the basis of lean production:
-
Flow - focuses on moving information and materials as close to customers as possible.
-
Value stream mapping - break down each stage of a process into discrete tasks and create a flowchart of the entire process;
-
Five S's: Sort, Shine Standardize, Sustain, Set In Order, Shine and Shine
-
Kanban: Use visual signals such stickers, colored tape, or any other visual cues, to keep track your inventory.
-
Theory of constraints: identify bottlenecks in your process and eliminate them using lean tools, such as kanban board.
-
Just-in time - Get components and materials delivered right at the point of usage;
-
Continuous improvement - Make incremental improvements rather than overhauling the entire process.