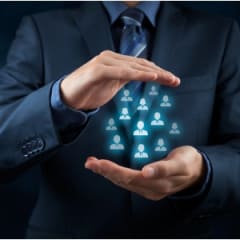
A risk assessment can help you assess whether or not your company is susceptible to potential dangers. An assessment should be performed on a regular basis. This will give you a current snapshot of the risks and threats posed by your system. Do a risk assessment on your application portfolio. Document security requirements, network diagrams. Data stored or transmitted by systems. Interactions with external services. Physical assets.
Hazard identification
Hazard identification is one of the most important steps in risk assessment. Many people lack the skills necessary to correctly identify hazards. This can lead to some valid risks being overlooked. Anchors are useful in identifying hazards, encouraging more people to do so and reducing the possibility of an overlooked risk. The study included 72 participants randomly assigned to high-anchor and low-anchor conditions. They also completed a five-factor personality test.
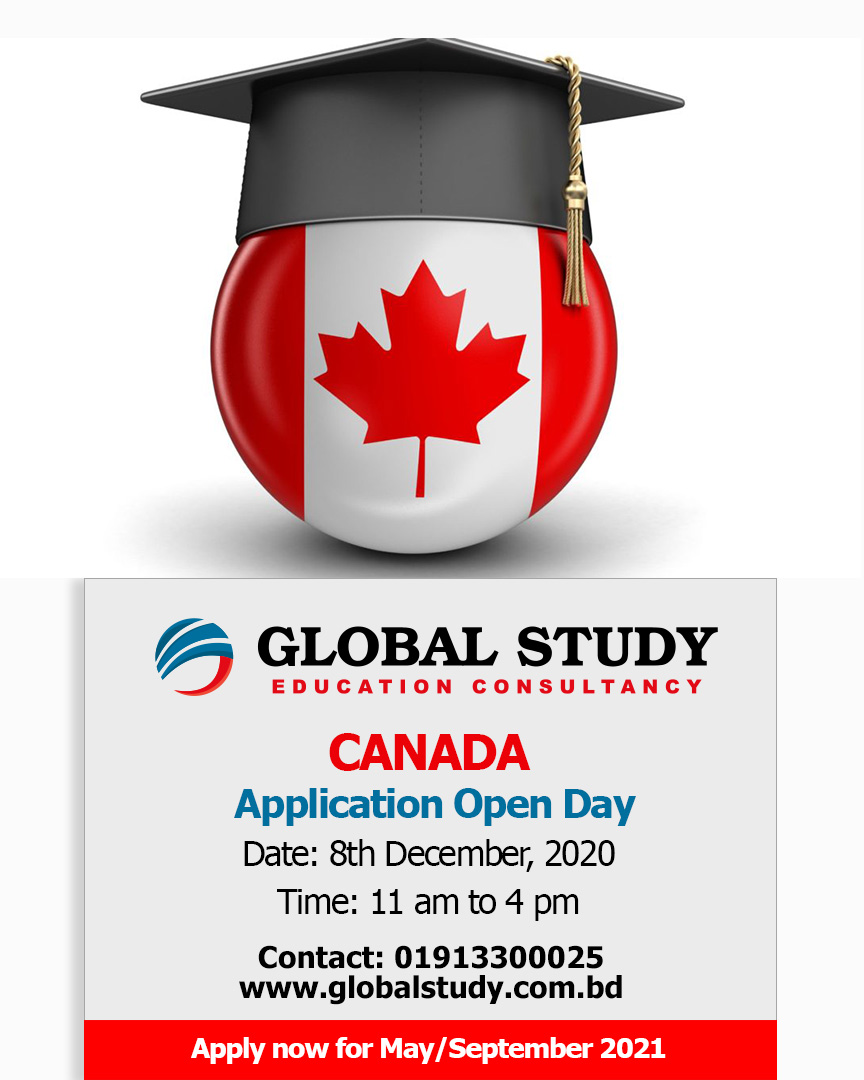
Document review
Ling is now a project manager at a large Internet company. Her initial project is creating privacy software for a client. Document review will be used to identify risks in projects. Document review is a structured review that examines the plans, assumptions, as well as all information available. This review will help inform the risk assessment process. In addition to identifying risks, documentation review can help to minimize risk exposure.
Influence diagrams
An effective tool for organizing a sequence, influence diagrams are useful. These diagrams are often used in risk management, project management, and other organizational disciplines. These diagrams enable participants to identify the connections between various factors and actions. This includes the possibility of harm or loss. These diagrams can also be used to assess the risk associated with specific projects. These diagrams are usually created in groups and may include examples.
Impact diagrams
An impact diagram is an effective tool to evaluate the relative risks involved in a project's risk assessment. They are a representation of the impact of each potential risk on the project. This analysis is usually performed by the project manager or someone who has knowledge of the risks. The results of the analysis are ranked by impact, duration uncertainty, and probability of occurrence. You can use the diagrams to identify which risks must be addressed first and which should be revised.
iAuditor
iAuditor, a digital tool to assess risk, replaces paper checklists and digital reporting. This software makes risk assessment more efficient and easier. To get started, you can download free templates. The checklists can also be modified to suit your needs. Your workers can then be assigned corrective measures. Once the assessment is complete comprehensive reports will automatically be generated and saved to you user account. These reports are available for sharing with others or can be updated as needed.
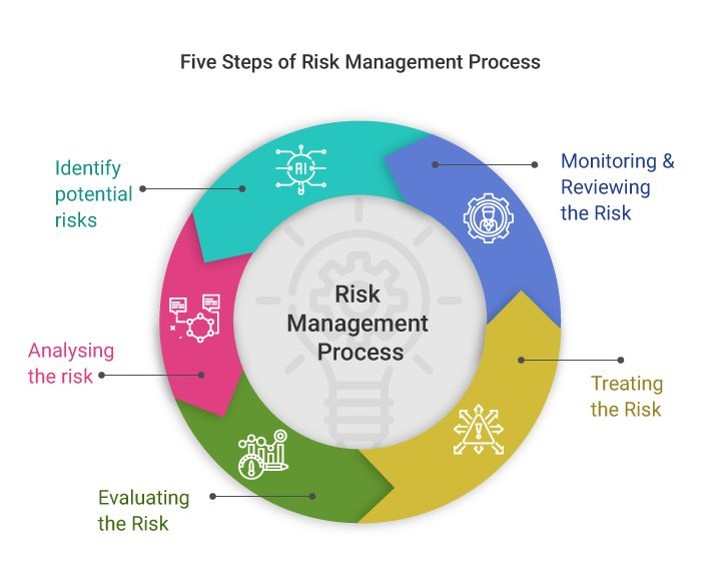
Corrective action
A corrective action refers to an appropriate response to a threat or possibility. The process can be very lengthy and time-consuming, and it's important to track the results to ensure that the action is successful. Additionally, corrective actions aren't isolated events, but rather part of the overall flow of operations. The ability to track the progress on corrective actions allows you to identify potential issues and decide which ones should be addressed. This will allow you to improve your overall performance.
FAQ
What is Six Sigma and how can it help you?
It's an approach to quality improvement that emphasizes customer service and continuous learning. The goal is to eliminate defects by using statistical techniques.
Motorola developed Six Sigma in 1986 to help improve its manufacturing processes.
This idea quickly spread throughout the industry. Today, many organizations use six sigma methods for product design, production and delivery.
What is Kaizen and how can it help you?
Kaizen is a Japanese term meaning "continuous improvement." It is a philosophy that encourages employees to constantly look for ways to improve their work environment.
Kaizen is based on the belief that every person should be able to do his or her job well.
What are management concepts?
Management Concepts are the principles and practices managers use to manage people and resources. These include topics such as human resource policies and job descriptions, performance assessments, training programs and employee motivation.
What kind of people use Six Sigma
Six-sigma will be well-known to anyone who has worked in operations research or statistics. However, anyone involved in any aspect of business can benefit from using it.
Because it requires a high level of commitment, only those with strong leadership skills will make an effort necessary to implement it successfully.
What's the difference between Six Sigma and TQM?
The main difference between these two quality-management tools is that six-sigma concentrates on eliminating defects while total QM (TQM), focuses upon improving processes and reducing expenses.
Six Sigma can be described as a strategy for continuous improvement. This approach emphasizes eliminating defects through statistical methods like control charts, Pareto analysis, and p-charts.
This method attempts to reduce variations in product output. This is done by identifying root causes and rectifying them.
Total quality management refers to the monitoring and measurement of all aspects in an organization. It also includes the training of employees to improve performance.
It is frequently used as an approach to increasing productivity.
Statistics
- UpCounsel accepts only the top 5 percent of lawyers on its site. (upcounsel.com)
- The average salary for financial advisors in 2021 is around $60,000 per year, with the top 10% of the profession making more than $111,000 per year. (wgu.edu)
- This field is expected to grow about 7% by 2028, a bit faster than the national average for job growth. (wgu.edu)
- Your choice in Step 5 may very likely be the same or similar to the alternative you placed at the top of your list at the end of Step 4. (umassd.edu)
- As of 2020, personal bankers or tellers make an average of $32,620 per year, according to the BLS. (wgu.edu)
External Links
How To
How is Lean Manufacturing done?
Lean Manufacturing methods are used to reduce waste through structured processes. They were created by Toyota Motor Corporation in Japan in the 1980s. The goal was to produce quality products at lower cost. Lean manufacturing emphasizes removing unnecessary steps from the production process. It is composed of five fundamental elements: continuous improvement; pull systems, continuous improvements, just-in–time, kaizen, continuous change, and 5S. Pull systems involve producing only what the customer wants without any extra work. Continuous improvement means continuously improving on existing processes. Just-intime refers the time components and materials arrive at the exact place where they are needed. Kaizen means continuous improvement, which is achieved by implementing small changes continuously. Fifth, the 5S stand for sort, set up in order to shine, standardize, maintain, and standardize. These five elements are used together to ensure the best possible results.
Lean Production System
Six key concepts are the basis of lean production:
-
Flow is about moving material and information as near as customers can.
-
Value stream mapping - Break down each stage in a process into distinct tasks and create an overview of the whole process.
-
Five S's - Sort, Set In Order, Shine, Standardize, and Sustain;
-
Kanban: Use visual signals such stickers, colored tape, or any other visual cues, to keep track your inventory.
-
Theory of Constraints - Identify bottlenecks in the process, and eliminate them using lean tools such kanban boards.
-
Just-in-time delivery - Deliver components and materials right to your point of use.
-
Continuous improvement is making incremental improvements to your process, rather than trying to overhaul it all at once.