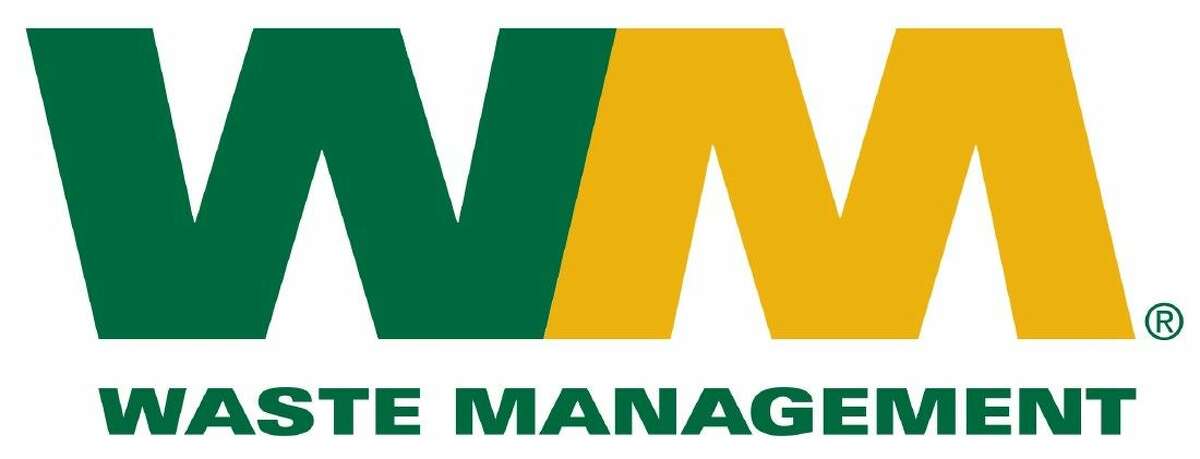
Perhaps you're wondering about project risk management if you've just been hired to work on a project. Here are some key components: Identifying risks, creating mitigation plans, monitoring progress and managing resources. In short, project risk management is a crucial part of your project. You don't need to know much about it. Read on to learn how you can make your project more profitable.
Identifying and assessing potential risks
It is important to identify potential risks in project-risk management as part of any risk assessment process. You can do this using a variety of methods, including brainstorming or interviews. The risk breakdown structure is an excellent way to validate and collect potential risks. You can also refer to historical project data in order to identify problems that were solved. But it is vital to fully understand all risks involved before you begin the process of risk management.
Your team should first review the scope, cost estimate, schedule, technical maturity and key performance parameters of the project to identify potential risks. Next, consider stakeholder expectations. After you have reviewed all aspects, decide if the current project plan is built on the identified risks. Then, look for strengths and weaknesses. It is also possible to review test event expectations. You should also consider security and safety risks.
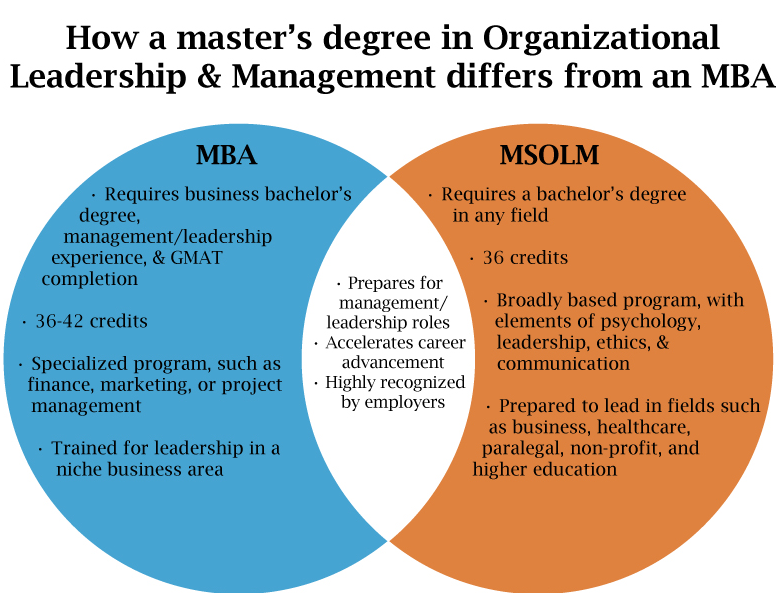
Develop a plan to reduce them
Planning to mitigate project risks involves careful consideration of all kinds of risk. Each risk has different consequences for the project and requires different strategies to address. Some risk types have less importance than others. This is why a risk management program that only addresses the most pressing risks is the best. As a risk mitigation plan is likely to be successful, it is vital that all parties are involved.
The first step to risk management is to determine and rate the risks. Every risk has the potential to have an impact on project scope and budget. By assessing its probability, a risk can be prioritized. Once the risks have been defined, the team will be able to determine the most appropriate response. It is possible to revise the plan following project completion or when additional information becomes available. It can also help to reclassify risk.
Monitoring progress
Regular meetings are essential for project managers to keep track of progress and discuss project risk management. You can set up such meetings weekly or monthly, or even at the beginning of each sprint, depending on your project's Agile methodology. These meetings should serve to identify risks, and make adjustments as needed. It is important that you are able to identify exceptions to your project's risk management processes. You can also reduce compliance costs with a project management system that identifies potential problems before they have an impact on the project's timeline or budget.
It is crucial to monitor progress in project risk management. It allows you to adjust your goals and keep your team on the right track. If the deadline is extended or your team is in trouble, you can extend it. Alternately, if your team's progress is good, you can extend the deadline. Analyzing progress will allow you to determine whether the project is on-track and whether it is a risky or successful.
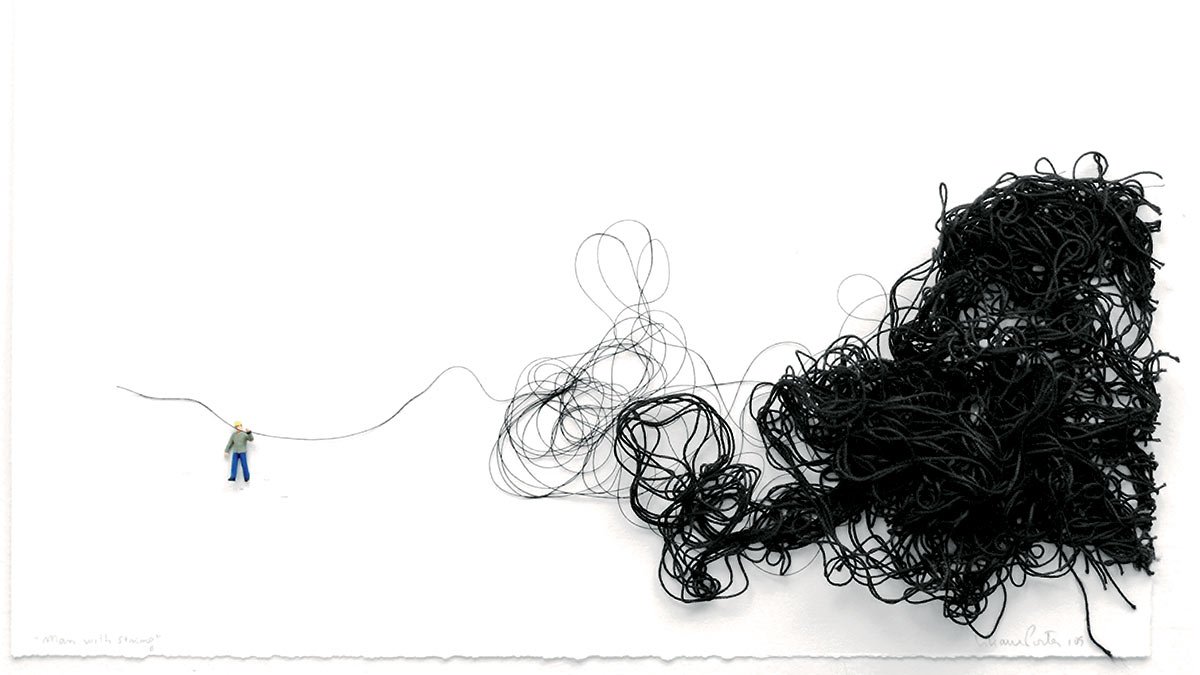
Monitoring resource use
You must monitor your resource usage as part of your project risk management process to ensure successful execution. To do this, create dashboards to visualize resource availability and skill sets and estimate the time needed to complete projects. It is just as important to monitor risks in the planning and execution stages as during actual execution. As the project moves forward, risks may materialize and become issues. These situations call for proactive preventive action.
The next step in managing risk is to analyze risks and determine their impact. After identifying and analyzing risks, the best course of action is to develop a strategy to resolve them. To ensure that the problem is resolved, the risk owner must be kept informed throughout the project. Monitoring resource use as part of project risk management is an iterative process. A risk can be considered severe or low-risk if it poses a higher-than-expected impact on the project.
FAQ
How to manage employees effectively?
Managing employees effectively means ensuring that they are happy and productive.
This also involves setting clear expectations and monitoring their performance.
Managers need to establish clear goals for their team and for themselves.
They need to communicate clearly and openly with staff members. They need to communicate clearly with their staff.
They also need to keep records of their team's activities. These include:
-
What was the result?
-
How much work did you put in?
-
Who did it all?
-
It was done!
-
Why it was done?
This information can be used for monitoring performance and evaluating results.
What are the five management process?
The five stages of a business include planning, execution (monitoring), review, evaluation, and review.
Setting goals for the future requires planning. Planning includes setting goals for the future.
Execution is when you actually execute the plans. You need to make sure they're followed by everyone involved.
Monitoring is the act of monitoring your progress towards achieving your targets. Regular reviews should be done of your performance against targets or budgets.
At the end of every year, reviews take place. They allow for an assessment of whether all went well throughout the year. If not, then it may be possible to make adjustments in order to improve performance next time.
Evaluation takes place after the annual review. It helps to identify what went well and what didn’t. It also provides feedback on how well people performed.
What are the steps to take in order to make a management decision?
Managers face complex and multifaceted decision-making challenges. It includes many factors such as analysis, strategy planning, implementation and measurement. Evaluation, feedback and feedback are just some of the other factors.
Management of people requires that you remember that they are just as human as you are, and can make mistakes. You can always improve your performance, provided you are willing to make the effort.
This video will explain how decision-making works in Management. We'll discuss the different types and reasons they are important. Managers should also know how to navigate them. You'll learn about the following topics:
Statistics
- The profession is expected to grow 7% by 2028, a bit faster than the national average. (wgu.edu)
- As of 2020, personal bankers or tellers make an average of $32,620 per year, according to the BLS. (wgu.edu)
- Your choice in Step 5 may very likely be the same or similar to the alternative you placed at the top of your list at the end of Step 4. (umassd.edu)
- Hire the top business lawyers and save up to 60% on legal fees (upcounsel.com)
- The BLS says that financial services jobs like banking are expected to grow 4% by 2030, about as fast as the national average. (wgu.edu)
External Links
How To
What is Lean Manufacturing?
Lean Manufacturing is a method to reduce waste and increase efficiency using structured methods. They were created by Toyota Motor Corporation in Japan in the 1980s. The aim was to produce better quality products at lower costs. Lean manufacturing focuses on eliminating unnecessary steps and activities from the production process. It is made up of five elements: continuous improvement, continuous improvement, just in-time, continuous change, and 5S. Pull systems allow customers to get exactly what they want without having to do extra work. Continuous improvement is constantly improving upon existing processes. Just-in-time is when components and other materials are delivered at their destination in a timely manner. Kaizen means continuous improvement. Kaizen involves making small changes and improving continuously. Last but not least, 5S is for sort. These five elements work together to produce the best results.
Lean Production System
Six key concepts are the basis of lean production:
-
Flow - focus on moving material and information as close to customers as possible;
-
Value stream mapping is the ability to divide a process into smaller tasks, and then create a flowchart that shows the entire process.
-
Five S's, Sort, Set in Order, Shine. Standardize. and Sustain.
-
Kanban - visual cues such as stickers or colored tape can be used to track inventory.
-
Theory of Constraints - Identify bottlenecks in the process, and eliminate them using lean tools such kanban boards.
-
Just-in Time - Send components and material directly to the point-of-use;
-
Continuous improvement - make incremental improvements to the process rather than overhauling it all at once.